赵桂英,王忠光,杨昭(徐州工业职业技术学院,江苏 徐州 221140)
摘要:采用低生热的补强配合体系, 对比研究了炭黑的种类、用量以及炭黑的并用配比对丁腈橡胶(NBR)
皮膜胶料性能的影响;对胶料硫化特性、力学性能及屈挠性能的测试结果表明,炭黑N660 的补强效果优于N774,炭黑的最佳用量为70份;随着N550/N660
并用配比中N550 用量的增加,胶料的拉伸强度、撕裂强度及屈挠性能逐渐提高;当N550/N660 配比在40/30~50/20 之间时,NBR
胶料的综合性能最好;考虑到NBR 胶料的性价比,确定40/30 为N550/N660 的最佳并用比。
关键词:炭黑;丁腈橡胶;皮膜;性能
中图分类号:TQ330.381 TQ333.7 文章编号:1009-797X(2014)20-0040-04 文献标识码:B
气动隔膜泵是一种新型流体输送机械, 是目前国内逐步推广应用的一种泵类。该泵采用压缩空气为动力源, 对于各种腐蚀性液体, 带颗粒的液体,
高黏度、易挥发、易燃、剧毒的液体, 均能予以抽光吸尽[1]。隔膜泵橡胶皮膜是一片碗状的内嵌增强织物的橡胶膜片, 安装于隔膜泵腔体中间, 边缘固定在泵体上,
由一边的动力源作用将膜片来回推动, 通过膜片的来回移动来改变隔膜泵另一边腔体的空间, 利用两片单向阀将流体( 水、化学液体等) 从泵的一端吸入,
向另一端排出[2]。因此, 要求隔膜泵橡胶皮膜具有一定的耐腐蚀性、良好的柔韧性、耐屈挠疲劳性, 低生热, 以提高隔膜泵橡胶皮膜的使用寿命。
丁腈橡胶(NBR) 是丁二烯与丙烯腈两种单体经乳液聚合得到的共聚物;其耐油、耐热、耐苯以及物理机械性能的优异性,
作为耐油橡胶制品的弹性体,广泛应用于航空航天、化工、汽车、石油开采、电线电缆、印刷、食品包装和纺织等领域[3]。橡胶制品中使用的填充补强剂占整个原材料的10%~15%,
其性能好坏直接影响产品的性能和质量以及产品成本,
橡胶制品中配合一定量的炭黑可以起到补强和填充作用以改善橡胶制品的性能。本研究以丁腈橡胶为主体材料,采用了低生热的补强配合体系,对比分析了炭黑的种类、用量以及不同炭黑的并用对NBR
皮膜胶料硫化特性、力学性能及屈挠性能的影响。
1· 实验部分
1.1 主要原材料
NBR-41 :兰化公司产品;N550 :卡博特快压出炭黑;N660
:卡博特通用炉黑;N774半补强炭黑:天津亿博瑞化工有限公司;氧化锌、硬脂酸:中国石化南京化工厂;促进剂、防老剂、软化剂等为市售产品。
1.2 基本配方
NBR 100 份(质量份,下同),氧化锌5 份,硬脂酸1 份,DOP 15 份,防老剂2.2 份,促进剂2 份, 硫磺0.5 份,
炭黑N660、N774、以及N660/N550 并用比均为变量。
1.3 主要设备与仪器
开放式炼胶机XK-160、平板硫化机QLB-50D/Q :无锡市第一橡塑机械有限公司产品;无转子硫化仪GT-M2000-A
:台湾高铁科技股份有限公司产品;高低温拉力试验机GT-AI-7000-GD
:台湾高铁科技股份有限公司产品;邵氏硬度计、摆锤式冲击弹性仪、屈挠试验机:江都市试验机械厂产品。
1.4 试样制备
1.4.1 混炼胶制备
用切胶机将丁腈橡胶切成便于加工的小块胶料,然后用16 寸的开炼机进行塑混炼,混炼过程及时调整冷却水流量, 使辊筒温度控制在65 ℃
以下。此次试验的加料顺序为:丁腈橡胶— 氧化锌— 硬脂酸— 防老剂、促进剂—炭黑—DOP— 硫磺, 待混炼均匀后下片, 停放[4]。
1.4.2 硫化试样制备
将混炼胶在室温放置24 h 后, 采用平板硫化机进行硫化试样的制备;硫化条件为,温度:160 ℃,时间:t90,压力:15
MPa。硫化后的试片在室温下停放12~36 h, 然后采用冲片机进行冲裁及性能测试。
1.5 性能测试[5]
硫化特性按GB/T16584—1996 橡胶用无转子硫化仪测定硫化特性进行, 实验条件为160 ℃, 压力为0.35 MPa~0.60 MPa
;拉伸性能按GB/T528—2009 硫化橡胶或热塑性橡胶拉伸应力应变性能的测试进行;撕裂性能按GB/T529—2008 硫化橡胶或热塑性橡胶撕裂强度的测定(
直角形) 进行;冲击弹性按GB/T1681—2006 硫化橡胶回弹性的测定进行;硬度按照GB/T 531—1999
硫化橡胶邵尔A硬度试验方法进行测试;屈挠性能采用GB/T13934—1992 硫化橡胶屈挠龟裂的测定进行。
2 ·结果与讨论
2.1 炭黑的种类及用量对NBR 皮膜胶料性能的影响
炭黑作为橡胶的主要补强剂, 其粒径、结构度和表面活性等对胶料的性能有重要的影响;本研究以丁腈橡胶配方为标准, 采用N660、N774
两种粒径较大的炭黑为补强剂,对比分析了炭黑的种类及用量对NBR 皮膜胶料性能的影响。本研究采用的炭黑配方如下表1 所示。
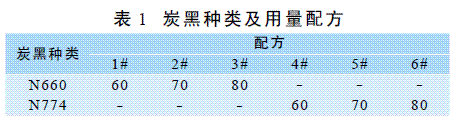
炭黑的种类及用量对NBR 胶料性能影响如下表2 所示。
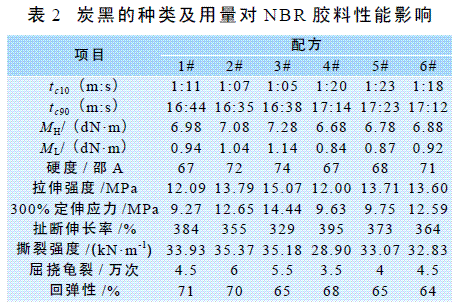
从表2 可以看出,6 个配方胶料的焦烧时间t10 均在1:05~1:23(m:s) 之间, 工艺正硫化时间t90 在16:35~17:23(m:s)
之间, 说明N660、N774 的用量对NBR 胶料的硫化特性影响不大。
从表2 还可看出, 随着炭黑用量的增加,NBR 胶料的邵氏硬度、拉伸强度、300% 定伸应力逐渐增加, 扯断伸长率逐渐降低;当炭黑用量相同时,N660
填充胶料的邵氏硬度、拉伸强度、300% 定伸应力均大于N774 填充胶,而扯断伸长率小于N774 填充胶;原因可能是N660 相对于N774
来讲,粒子较细,结构较高,易于在橡胶中的分散,
形成结合橡胶比例大,因此对橡胶的补强效果好于N770。胶料的撕裂强度随炭黑用量的增加先增加后基本保持不变,说明炭黑N660、N770 在一定用量范围内,
可以改善胶料的抗撕裂性能;6 个配方胶料的弹性均在64%~71% 之间,弹性较高,胶料柔韧性好,可能是N660、N774
粒子较粗,填充的比较松散,分子之间的空隙较大, 使得分子链之间的作用力减弱, 分子链的滑动能力增强, 受到外力冲击后,
具有较好的恢复变形能力。从胶料屈挠龟裂测试数据可以看出, 填充N660 胶料的屈挠次数明显大于填充N774 胶料,说明N660 填充胶的耐曲挠性能好。当N660
的用量为70 份时,NBR 胶料的综合性能最好。
2.2 炭黑并用对NBR 皮膜胶料性能的影响
粒径、结构及表面化学性质不同的两种炭黑并用, 分散过程中会互相影响, 能提高其在胶料中的的分散性及胶料的物理机械性能,
产生优势互补的效果;本研究将N550 与N660 两种炭黑并用,对比分析炭黑的并用比对NBR 填充胶料性能的影响。采用的炭黑并用配方如表3所示。
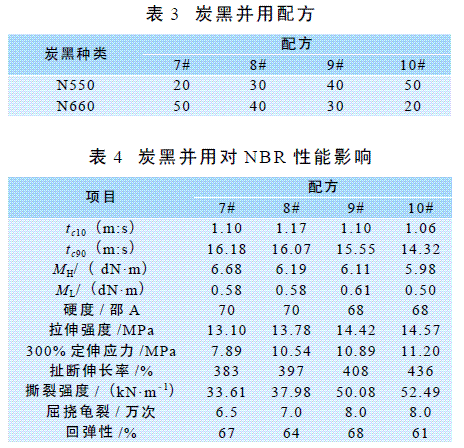
炭黑N550/N660 并用比对NBR 性能的影响见下表4。从表4 可以看出, 随着N550/N660 并用配比中N550
含量的增加,胶料的焦烧时间t10 和工艺正硫化时间t90 逐渐减少, 增加N550 的用量能缩短胶料的硫化时间, 但影响不大。
从表4 还可看出, 随着N550/N660 并用配比中N550 用量的增加, 胶料的拉伸强度、300% 定伸应力逐渐增加;当N550/N660
并用配比为50/20 时, 达到最大值;原因可能是N550 结构高,易分散,在软质炭黑中,其补强性能最高。胶料的硬度随着N550
用量的增加有所降低;而胶料的弹性先增加后降低, 但变化不大;随着N550/N660 并用配比中N550 用量的增加,
胶料的撕裂强度和屈挠性能有一定的提高。
与70 份N660 填充胶性能相对比, 当N550/N660 配比在40/30~50/20 之间时,
炭黑并用胶的拉伸强度、扯断伸长率较大;而硬度、300% 定伸应力、弹性小于N660 填充胶;并用胶的撕裂强度、屈挠性能明显大于N660
填充胶;说明N550/N660 炭黑并用产生了协同效应,提高了炭黑的分散性能,使胶料的抗撕裂性能、耐曲挠等性能得到改善。
3 ·结论
采用炭黑N660、N774 作为NBR 的填充补强剂,随着炭黑用量的增加,胶料的拉伸强度、300% 定伸应力逐渐提高;其中N660
的补强效果优于N774 ;当N660 用量为70 份时, 胶料的撕裂强度和屈挠性能达到最大值。
随着N550/N660 并用配比中N550 用量的增加, 胶料的拉伸性能、300% 定伸应力、撕裂强度及屈挠性能逐渐提高;当N550/N660
配比为40/30~50/20 之间时,NBR 胶料的综合性能最好;考虑到NBR 胶料的成本,确定N550/N660 的并用配比为40/30
时,胶料的性价比最高。
在NBR 皮膜胶料中,采用N550、N660 两种炭黑并用, 产生了协同效应, 提高了炭黑的分散性及硫化胶的物理机械性能。
参考文献:
[1]裴晋平. 气动隔膜泵在药品和与食品生产中的应用[ J ] .医药工程设计,2009,30(05) :23~26.
[2]邓治国. 隔膜泵高屈挠丁腈皮膜的研制[J] . 世界橡胶工业,2013,40(8) :34~37.
[3]王忠超. 丁腈橡胶性能影响因素[D]. 西北师范大学硕士学位论文,2012,05.
[4]翁国文. 配合与塑混炼操作技术[M]. 徐州:中国矿业大学出版社,2008,28~32.
[5]赵桂英,王忠光. 高分子材料性能测试技术[M]. 北京:化学工业出版社,2013.20~127.