高轶,赵素合(北京化工大学 材料科学与工程学院,北京 100029)
笔者采用甲基丙烯酸钠对白炭黑表面进行改性是因为一方面,甲基丙烯酸钠中有双键7T键,甲基p轨道与拨基中电子形成较为稳定的共扼体系,这种共扼体系有可能与锡偶联的溶聚丁苯橡胶中的苯环的大7T键体系产生相互作用,使得能量降低,从而与橡胶的相容性较好;另一方面,甲基丙烯酸钠中的O带负电荷,且有孤对电子,而白炭黑的硅轻基中的H带正电荷,在反应条件允许的情况下,白炭黑中的硅轻基会进攻甲基丙烯酸钠中的拨基,从而使白炭黑的表面能降低,使白炭黑在胶料中很好地分散。而且在此反应中,附产物是水,对环境不会造成污染。
在以前的实验中,笔者研究了甲基丙烯酸钠对锡偶联的溶聚丁苯橡胶的性能的影响。根据纳米增强的成因目前认为,在交联过程中,甲基丙烯酸钠在橡胶基质中能够原位生成纳米粒子(聚甲丙烯酸金属盐),从而对橡胶产生优异的纳米增强效果。聚甲基丙烯酸钠(PMMANa)纳米粒子在SSBR-2305中的形成过程可简要描述为:在交联过程中,甲基丙烯酸钠在过氧化物(DCP)的作用下,一方面发生自聚合,形成纳米级的聚甲基丙烯酸钠粒子;一方面与溶聚丁苯橡胶大分子产生接枝和交联。这个过程类似于橡胶的乳液聚合机理。聚甲基丙烯酸钠粒子的大小决定于DCP、交联温度、溶聚丁苯橡胶等因素。原生粒子极小的直径和与橡胶大分子间的化学键合(不一定是全部粒子)是甲基丙烯酸钠对溶聚丁苯橡胶起增强作用的主要原因[l-3〕。
1实验
1.1试验配方
锡偶联的SSBR一2305 100(北京燕山石化股份有限公司),氧化锌4.0;硬脂酸1.0;防老剂RD 1 .5,促进剂DM 1.2,促进剂D
0.6,硫化剂DCP变量,白炭黑变量(台湾南帝化学工业股份有限公司)。
1.2试样制备
混炼及硫化:在功16OX320型双辊开炼机上混炼。硫化温度160℃,用25t电热平板硫化机压制硫化试样。
1.3性能表征
混炼胶经液氮冷却后击断,硫化胶在常温下切断,用英国剑桥公司制造的S一250一111型扫描电子显微镜观察它们的SEM形态。各项物理机械性能按GB/T
528一82测试。
2实验结果与讨论
在试验中,笔者对试验工艺、交联温度、过氧化物DCP的用量、甲基丙烯酸与氢氧化钠的当量比、甲基丙烯酸钠的用量对硫化胶的性能进行了研究。发现实验工艺采用原位酸碱交替加料工艺、硫化温度为160℃、DCP为1.2份、酸碱当量比为
1.25:1时硫化胶的性能达到最佳。故在此基础上,对甲基丙烯酸钠并用增强锡偶联的溶聚丁苯橡胶进行研究[5]。
2.1反应工艺对硫化胶性能的影响
试验中,笔者首先对在混炼过程中,甲基丙烯酸钠与白炭黑的加料顺序对胶料的补强作用进行了研究,发现先加白炭黑,后原位生成白炭黑的方法较好。而在此方法中,笔者进一步进行了研究,具体工艺如下:
2.1.1混炼工艺一

2.1.2混炼工艺二
SSBR包辊→加白炭黑→酸碱交替 加,不打三角包→争加各种助剂,打4个三角包 →加DCP,打7个三角包
2.1.3混炼工艺三
SSBR包辊→加白炭黑→加酸,打7个 三角包→加碱,打7个三角包→加各种 助剂,打7个三角包→枷加DCP,打7个三角包
2.1.4混炼工艺四
SSBR包辊→加白炭黑→加碱,打7个 三角包→加酸,打7个三角包→枷加各种助剂,打7个三角包→枷加DCP,打7个三角包
2.1.5混炼工艺五
SSBR包辊→加白炭黑→,加酸,不打 三角包→加碱,打7个三角包→枷加各种助剂,打7个三角包→加DCP,打7个三角包
2.1.6混炼工艺六
SSBR包辊→加白炭黑→,加碱,不打 三角包→加酸,打7个三角包→枷加各种助剂,打7个三角包→加DCP,打7个三角包
在上述混炼工艺中,我们发现工艺二为最佳,因为先加入白炭黑,使白炭黑在生胶中达到一定程度的分散,后酸碱交替加料(先加酸),酸碱交替加的目的是为了提高酸碱转化率,甲基丙烯酸钠微粒在向橡胶分散的过程中,与白炭黑粒子相互作用,将白炭黑表面改性,使白炭黑粒子达到纳米级的分散。
2.2甲基丙烯酸钠与白炭黑不同配比并用对硫化胶性能的影响
本实验研究了白炭黑、甲基丙烯酸钠不同配比对硫化胶的物理机械性能的影响。
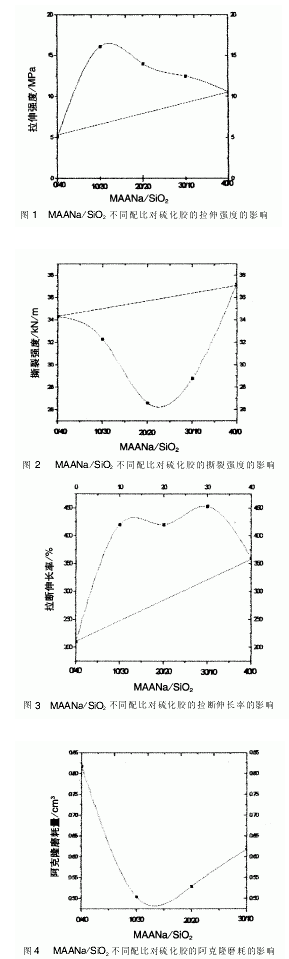
从图中可以看出,甲基丙烯酸钠与白炭黑并用后补强橡胶,二者有相互促进作用,尤其在二者的质量比达到10/30时,拉伸强度达到16.1 MPa。
对于撕裂强度,甲基丙烯酸钠与白炭黑并用以后,二者对于橡胶的补强产生负面效应,只加甲基丙烯酸钠40份时,硫化胶的撕裂强度可以达到37.2
kN/m,当二者质量比为10/30时,撕裂强度为32.3
kN/m,这说明甲基丙烯酸钠对硫化胶的撕裂强度的影响很大,在此基础上,笔者还将20份甲基丙烯酸(MAA)和20份白炭黑并用来补强橡胶,撕裂强度只有20
kN/m。这可能是因为甲基丙烯酸钠与丁苯橡胶发生交联反应,形成了键能高的离子键桥键,增加了交联键数目;同时甲基丙烯酸钠还可发生均聚,形成微细分散的刚性均聚微区对SSBR硫化胶具有一定的增强作用,这样使得硫化胶撕裂强度提高。
对于拉断伸长率,在甲基丙烯酸钠与白炭黑并用的三个试验中,可以发现拉断伸长率变化不大,而单纯加MAANa和5102时,拉断伸长率不大,这可能是因为在过氧化物
DCP交联作用下,纯的填料补强橡胶时,高分子链相互的交联密度增大,所以拉断伸长率不高。
对于阿克隆磨耗,白炭黑填充的硫化胶的阿克隆磨耗量较高,达到0.818 cm3当添加了甲基丙烯酸钠以后,阿克隆磨耗量降低。
2.3工艺改进后对硫化胶性能的影响
从以上分析,我们可以看出当甲基丙烯酸钠与白炭黑的质量比为20/20、10/30时,硫化胶的性能比较好,所以为了进一步提高硫化胶的性能,笔者改进了工艺。
考虑到甲基丙烯酸与氢氧化钠反应时生成的水对硫化胶的性能产生直接的影响,所以在生胶未硫化前,在开炼机的双辊上出一层很薄的片,然后放入烘箱中,烘适当的时间再去硫化。实验结果发现,被烘过的胶料性能较好,质量比为10/30的硫化胶的拉伸强度可到达16.4
MPa,撕裂强度为39.2
kN/m,拉断伸长率500%,阿克隆磨耗量降到0.361C耐。这可能是由于一方面在烘的过程中,温度较高,提高了酸碱的转化率,而酸碱转化率直接影响到胶料的性能;另一方面,温度升高可除去胶料中的部分水,水的存在对硫化胶性能的负面影响很大,因为生胶中有水分在硫化的过程中,水分并不能有效地除去,硫化胶中就会有缺陷。
3结论
A采用甲基丙烯酸钠对白炭黑表面进行改性是一种新型的方法。
B原位生成甲基丙烯酸钠与白炭黑并用在填充胶料的过程中,混炼工艺对硫化胶的性能影响很大,采用先填充白炭黑,然后酸碱交替加料生成甲基丙烯酸钠(先加酸)的工艺为最佳工艺。
C原位生成甲基丙烯酸钠与白炭黑并用的方法对锡偶联的溶聚丁苯橡胶补强时,二者起到互相促进的作用。
D改进工艺后,甲基丙烯酸钠与白炭黑的质量比为10/30时,硫化胶的拉伸强度为16.4 MPa,撕裂强度为39.2
kN/m,拉断伸长率500%,阿克隆磨耗量降到0.361 cm,。
E甲基丙烯酸钠与白炭黑并用填充加料后,在“绿色轮胎”、“彩色轮胎”方面很有前途。
参考文献
[1]于伯龄,姜胶东.实用热分析[M].北京:纺织工业出版社, 1990.
[2]神户博太郎.热分析[M].北京:化学工业出版社,1981.【3〕Perkin一Elmer Corporation.Thermal
Analysis Newsletter, 1970(9).
[4]赵阳等.ZDMA/NBR纳米复合材料的性能研究[J].合成 橡胶工业,2002,49(l):9一14.
[5〕高轶,赵素合.原位生成聚甲基丙烯酸钠增强锡偶联溶聚丁苯橡胶的研究[J].橡塑资源利用,2005(2):9一12.