黄舟a,项可璐a,杨磊a,吴友平a,b( 北京化工大学a. 北京市新型高分子材料制备与加工重点实验室; b. 有机无机复合材料国家重点实验室,北京100029)
摘要:对于炭黑/丁苯橡胶复合材料,用5 份白炭黑、黏土和淀粉分别等量替代炭黑,研究了复合材料在宽广应变范围( 30% ~ 100%)
的疲劳破坏性能。结果表明,30%应变下,加入黏土胶料的疲劳寿命提高了1 倍; 100%应变下,加入白炭黑胶料的疲劳寿命提高了1
倍;加入淀粉胶料的疲劳寿命下降。原因是由于在30%的应变下,加入黏土提高了复合材料的滞后能,而生热不大,且片层状黏土对裂纹扩展有较强的阻碍作用;加入白炭黑胶料的滞后能不变,由于白炭黑的粒径小于炭黑,抗裂纹能力提高,因而在所研究的应变范围内其抗疲劳破坏性能提高;由于淀粉的粒径是微米级的,且加入淀粉后复合材料的滞后能降低,因此其抗疲劳破坏性能降低。
关键词:丁苯橡胶;填料;复合材料;疲劳破坏;撕裂能;滞后能;机理
中图分类号: TQ 333. 1 文献标志码: A 文章编号: 1000-1255( 2013) 04 -0268-06
橡胶复合材料的疲劳破坏性能关系着橡胶制品的使用寿命、安全性和可靠性,因此研究橡胶复合材料的疲劳破坏性能有重要意义。材料的疲劳破坏是材料在动态使用条件下,由裂纹增长至材料断裂的过程。Rivlin
等[1]最早将断裂力学应用于橡胶材料的疲劳破坏研究,并将裂纹每增长单位面积所释放的能量称为撕裂能。Lake[2]研究了天然橡胶和丁苯橡胶硫化胶的疲劳裂纹增长速率与撕裂能的关系曲线,分为4
个区域: ( 1) 撕裂能很小时,没有裂纹增长,疲劳裂纹增长速率为一个常数; ( 2) 撕裂能达到一定值后,裂纹开始增长,疲劳裂纹增长速率与撕裂能呈线性关系;
( 3) 撕裂能继续增大,疲劳裂纹增长速率与撕裂能呈指数关系; ( 4) 撕裂能很大时,疲劳裂纹增长速率趋于无穷大。
材料疲劳破坏是一个复杂的动态累积过程,受到多方面因素的影响,例如材料的定伸应力[3],在定应变条件下,材料定伸越大,其受到的应力就越大,因而每个疲劳周期,外界输入的能量越多,材料的抗疲劳破坏性能越差。此外还有橡胶类型、填料、频率和温度等影响因素[4
- 6]。但关于不同形状系数填料对橡胶复合材料抗疲劳破坏性能影响的研究很少,因而本工作着重研究加入少量的不同填料( 黏土、白炭黑和淀粉)
对宽广应变范围内炭黑/丁苯橡胶复合材料抗疲劳破坏性能的影响,并分析其中的作用机理。
1· 实验部分
1. 1 原材料
丁苯胶乳和丁苯干胶,牌号ESBR 1502,吉林石化公司有机合成厂产品。炭黑,牌号N 234,天津卡博特化工有限公司产品。白炭黑,牌号VN
3,青岛德固赛有限公司产品。钠基黏土,吉林省四平市膨润土厂产品。蜡制玉米淀粉( 纯支链) ,山东华农特种玉米开发有限公司产品。其他试剂均为市售工业品。
1. 2 配方
制备添加少量不同填料的炭黑/丁苯橡胶复合材料试样的配方如表1 所示,其中对试样C
4淀粉配方的促进剂和硫黄用量进行了调整,因为淀粉的加入会大大降低交联密度,使得材料的100%和300% 定伸应力降低,经过调整后4
个配方的交联密度相近,这样能使得应力较为一致,尽量排除其干扰,然后从能量的角度来分析填料的影响。
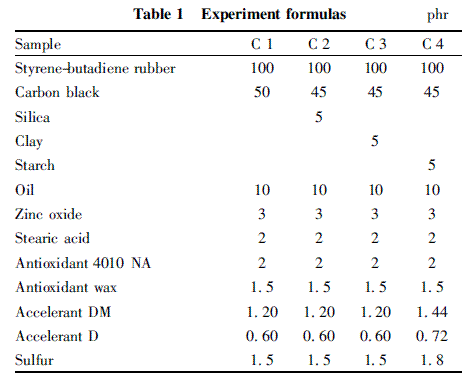
1. 3 试样制备
黏土母胶 将一定量的黏土加入到去离子水中,剧烈搅拌8 h,沉降24 h,得到稳定的悬浮液。取上层清液测定固体物含量后,量取配置量,加入界面剂搅拌5
min,再加入丁苯胶乳搅拌20 min后,用1% 的硫酸溶液絮凝,洗涤至中性, 50 ℃下烘干48 h 制得黏土母胶。
淀粉母胶 将一定量的淀粉加入到去离子水中,加热到90 ℃左右搅拌30 min,得半透明状的淀粉糊。然后与丁苯胶乳混合搅拌30 min,用1.
5%的氯化钙溶液絮凝,洗涤, 50 ℃下烘干48 h制得淀粉母胶。
混炼与硫化 试样C 3 和试样C 4 中的黏土和淀粉是通过上述黏土母胶( 丁苯胶乳与黏土质量比为5 /1) 和淀粉母胶( 丁苯胶乳与淀粉质量比为5
/1) 的形式混入的,以保证黏土和淀粉在丁苯橡胶中的均匀分散。在上海橡胶机械一厂生产的Φ160 × 320 冷辊开炼机上按常规橡胶混炼工艺制备4
种混炼胶。通过北京环峰机械厂生产的P 3555 B 2 型硫化仪测定正硫化时间,然后用上海橡胶机械制造厂生产的XQLB - 350 × 350
型平板硫化机进行硫化,硫化温度150 ℃,时间取正硫化时间。
1. 4 分析与测试
填料网络结构 用美国Alpha 科技有限公司生产的RPA 2000 型橡胶加工分析仪对混炼胶进行应变扫描,试验条件为: 100 ℃,1 Hz。
物理机械性能 硫化胶的拉伸性能和撕裂强度用深圳新三思计量技术有限公司生产的CMT4104 型电子拉力机分别按照ASTM D 412 和ASTM D
624 测试。
疲劳裂纹增长性能 用江苏明珠试验机械厂生产的MZ - 4003 B 型立式疲劳机对复合材料进行疲劳裂纹增长性能的测试。试样为长条状,长100
mm,宽15 mm,厚2 mm。试验条件为: 温度25 ℃,频率5 Hz,应变分别为30%、50%、70%、80%、90%和100%。试样先预拉2 000
个周期,然后在试样长边的中间处割1 mm 的预割口再进行试验,记录裂纹长度与疲劳周期。
撕裂能 用深圳新三思计量技术有限公司生产的CMT 4104 型电子拉力机测定试样的撕裂能,温度为25 ℃,拉伸速率为20
mm/min。本工作所用测定撕裂能的试样为长条状样条( 见图1) ,规格同疲劳裂纹增长性能所用样条,称为拉伸样条[1 - 2,7-
8],对应的计算撕裂能的公式如式( 1) 所示。
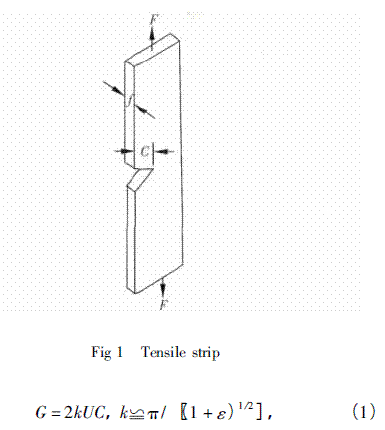
式中: G 为撕裂能; k 为系数; U 为应变能密度; C为裂纹长度; ε 为应变。由式( 1)
可以看出,要计算撕裂能,首先必须测定应变能密度。应变能密度由应力- 应变曲线中回缩曲线下的积分面积算出,如图2
中黑色部分所示,因为这部分能量在拉伸过程中是先储存在材料中,最后释放回环境中的[3]。测定某应变的应变能密度时,先将样条在相应应变下预拉伸4
次,消除Mullins 效应,然后割口,进行第5 次拉伸,根据第5 次拉伸的应力-应变曲线计算其应变能密度。
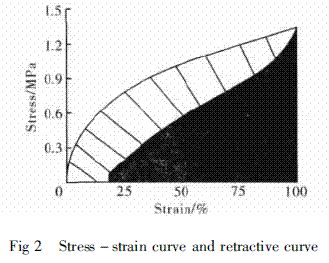
滞后能密度 与撕裂能试验样条相同,其滞后能密度为图2 中滞后环的大小,如图2 中斜线部分所示。
2· 结果与讨论
2. 1 硫化特性
由图3 和表2 可以看出,与炭黑胶料试样C 1相比,分别加入白炭黑和黏土的试样C 2 和试样C 3 的转矩差降低,即交联密度降低; 加入淀粉的试样C
4 的转矩差提高,即交联密度提高,而且试样C 4
的焦烧时间也有所缩短,主要是由于硫化剂用量较多的缘故,说明通过调整硫化剂用量来使交联密度达到完全一致还存在一定的困难。与试样C 1 相比,试样C 2 和试样C
3
的正硫化时间有所延长,表明白炭黑和黏土均具有一定迟延硫化的作用。不同填料会对硫化体系产生不同的影响,本工作中所添加填料的用量很少,所以影响不大,测试硫化特性主要是为了了解交联密度的大小。
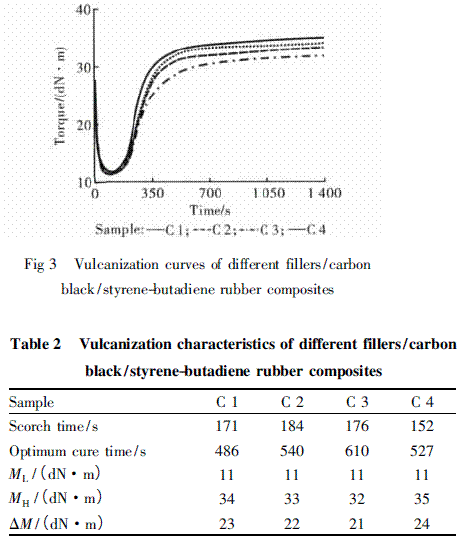
2. 2 填料网络结构
由图4 可以看出,与试样C 1 相比,试样C 2和试样C 3 的Payne 效应增强,试样C 4
减弱。分析原因认为,4个胶料的主要填料网络是炭黑,加入5
份黏土后,黏土片层长宽为几百纳米,受到外力作用时炭黑网络会受到黏土片层的阻碍,使得整个填料网络运动受限,刚性增大,初始模量增加,因此Payne 效应增强;
对于加入白炭黑的体系而言,白炭黑VN 3 的平均粒径为14 nm,而炭黑N 234 的平均粒径为22
nm,白炭黑粒径比炭黑小,比表面积相对较大,形成网络结构的能力比炭黑强,所以加入5 份白炭黑后Payne 效应也增强;但淀粉粒径在微米级别,加入5
份淀粉后,其复合材料的Payne 效应减弱。
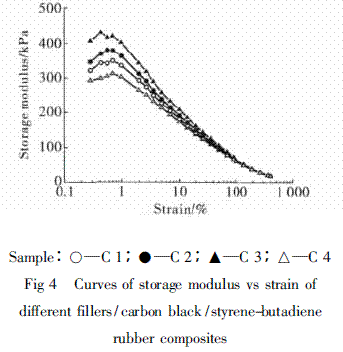
2. 3 物理机械性能
由表3 可以看出,与试样C 1 相比,试样C 3和试样C 4 的100%和300%定伸应力较大,试样C 2 不变。对于定应变条件的疲劳过程而言,试样C
3 和试样C 4 受到的应力可能要大于试样C 1和试样C 2,这对于试样C 3 和试样C 4 的抗疲劳破坏性能是不利的。与试样C 1 相比,试样C 2
的拉伸强度略有提高,试样C 3 的撕裂强度有所提高,试样C 4 的撕裂强度和扯断伸长率略有下降。这与白炭黑的粒径较小、淀粉的粒径较大且试样C 4
的配方中硫化剂用量较大,而黏土为层状结构的特性相吻合。
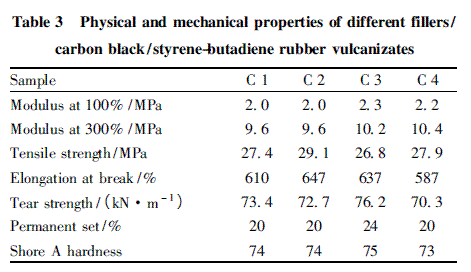
另外,由硫化特性和物理机械性能可以看出,试样C 4
的硫化剂用量较高,其交联密度最大,扯断伸长率最低,这也将对加入淀粉复合材料的抗疲劳破坏性能产生影响。下面即从应力和能量两个角度加以分析,从应力角度主要分析的是硫化剂的作用,从能量角度主要分析的是填料的作用。
2. 4 疲劳裂纹增长性能
测试了30% ~ 100% 应变内复合材料的疲劳寿命与应变的关系,结果如图5 所示。从图5 可以看出,与试样C 1
相比,在所测试的应变范围内,加入白炭黑后复合材料的疲劳寿命提高,加入淀粉后疲劳寿命降低; 加入黏土后,在50%
~100%应变下,复合材料的疲劳寿命基本不变,但在30%的小应变下疲劳寿命明显提高,抗疲劳破坏性能最好。所以,在小应变下加入黏土后复合材料的疲劳性能最好,在大应变下加入白炭黑后最好,而无论在小应变还是大应变下,加入淀粉后复合材料的疲劳性能都变差,这可能是因为试样C
4 中淀粉的粒径较大,且复合材料定伸应力也较大的缘故( 定应变下,定伸应力大则输入的能量高) 。
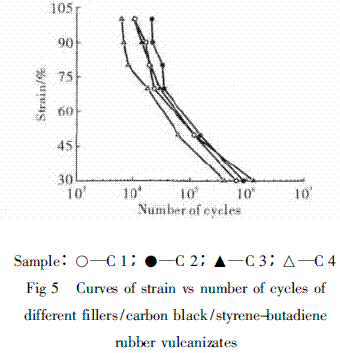
由图5 还可以看出,在50%、70%、80%、90%和100%应变下,4种复合材料疲劳裂纹增长性能好坏的变化规律是相同的,而在30%
应变下,加入黏土胶料的疲劳性能最好,因此随后研究了100%和30%应变下裂纹增长与疲劳寿命的关系,结果见图6。由图6( a) 可以看出,在100%
应变下,与试样C 1 相比,试样C 2 的裂纹增长速率明显变慢,疲劳寿命提高了1 倍; 试样C 4 的裂纹增长速率最快,试样C 4 的疲劳寿命降低了1
倍;试样C 3 的裂纹增长速率和疲劳寿命基本无变化。由图6( b) 可以看出,在30% 应变下,与试样C 1 相比,试样C 2 和试样C 3,尤其是试样C 3
的裂纹增长速率明显降低。
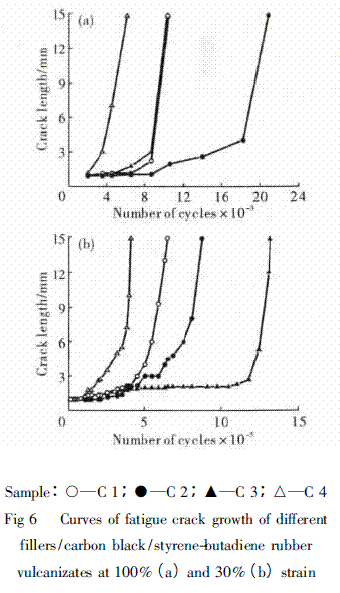
为了明确应变对疲劳裂纹增长速率的影响,将不同应变下的初始裂纹增长速率与应变做图,结果如图7 所示。从图7 可以明显看出,应变对试样C 3
的裂纹增长速率影响最大,尤其是在30% ~ 50%的应变范围内; 在所研究的应变范围内,试样C 2 的裂纹增长速率均低于试样C
1,表明白炭黑与黏土对炭黑/丁苯橡胶复合材料裂纹增长速率的影响明显不同。
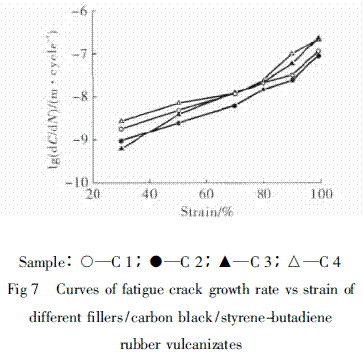
如前所述,在定应变下,炭黑/丁苯橡胶复合材料的定伸应力对其抗疲劳破坏性能的影响较大,为了减少复合材料定伸应力的影响,下面将从能量和形貌的角度加以分析。
2. 5 滞后能对疲劳性能的影响
4 种材料在6 个应变下的滞后能密度如表4所示。从表4 可知,与试样C 1 相比,试样C 2的滞后能密度不变,试样C 3 提高,试样C 4
降低。这与前述分析的填料网络结构强弱的顺序基本一致: 加入黏土后填料网络结构增强,滞后能提高; 加入淀粉后网络结构减弱,滞后能降低,同时由于试样C 4
较高的交联密度阻碍了橡胶交联网络的运动,也使其滞后能降低。结合上述加入黏土复合材料在30%
小应变下抗疲劳破坏性能明显提高、而在大应变下裂纹增长速率明显加快的现象,分析原因如下:
在小应变下,滞后能越大则外界输入的能量消耗在滞后生热上的越多,这样用于裂纹增长的能量就小;同时由于小应变下生热较小,可以快速地耗散到环境中,不会因为温升导致化学降解加速。可是在大应变下,由于滞后能的提高,生热增大并累积,不能快速地耗散到环境中,温升导致材料性能变差,因而裂纹增长速率加快。
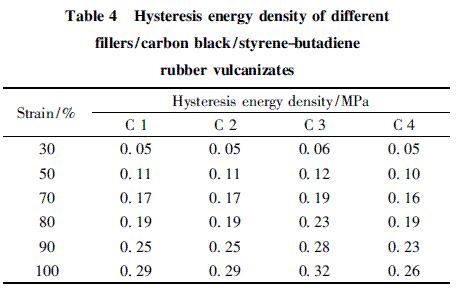
2. 6 撕裂能与裂纹增长速率的关系
添加少量填料的炭黑/丁苯橡胶复合材料疲劳裂纹增长速率与撕裂能的关系曲线见图8。从图8
可以看出,在能量较小时复合材料的撕裂能与裂纹增长速率呈指数关系,撕裂能较大时裂纹增长速率迅速增大,趋于无穷,与文献[2]中提到的第3 和第4 区域相符(
如图中的Ⅲ区域和Ⅳ区域所示) 。在指数关系区,与试样C 1 相比,试样C 2 的曲线基本处于试样C 1 之下,说明在同一撕裂能下试样C 2
的裂纹增长速率要小于试样C 1,即加入白炭黑后胶料的抗裂纹增长能力提高,这是因为白炭黑粒径小于炭黑的缘故; 试样C 3
曲线的斜率最大,说明撕裂能较小时加入黏土后胶料的抗裂纹增长能力提高; 试样C 4 的曲线位于试样C 1
之上,这是因为淀粉的粒径大于炭黑且材料的滞后能较低的缘故。
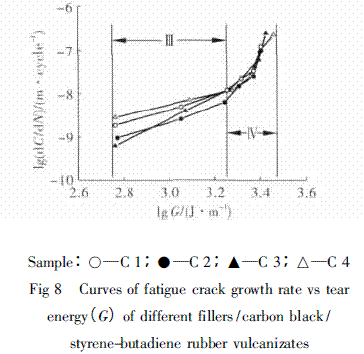
在裂纹增长速率迅速增加的第4 区,4
种复合材料的曲线基本重合,说明撕裂能增加到一定程度后,材料抗疲劳破坏的能力大大减弱,不同类型填料的影响已不明显。
3 ·结论
a) 对于炭黑/丁苯橡胶复合材料而言,在30%的小应变下,加入黏土后其疲劳寿命提高1倍; 在30% ~ 100%
应变范围内,加入白炭黑后疲劳寿命提高,加入淀粉后疲劳寿命降低。
b) 在小应变下,加入黏土后炭黑/丁苯橡胶复合材料的滞后能增加,黏土片状结构抗裂纹增长的优势可以充分体现。
c) 白炭黑的加入虽然不改变材料的滞后能,但白炭黑的粒径较小,仍明显提高了炭黑/丁苯橡胶复合材料的抗疲劳破坏性能。
参考文献:略