马建华1,吴友平1,2(1.北京化工大学有机无机复合材料国家重点实验室,北京 100029;2.北京化工大学北京市新型高分子材料制备与成型加工重点实验室,北京 100029)
摘要:对比研究采用相同体积分数的炭黑和白炭黑分别补强溶聚丁苯橡胶(SSBR)和乳聚丁苯橡胶(ESBR)胎面胶的性能。试验结果表明:与炭黑填充丁苯橡胶(SBR)胶料相比,经偶联剂Si69(用量为白炭黑用量的8%)热处理的白炭黑填充SBR胶料的分散性改善,硫化胶的300%定伸应力增大,拉断伸长率减小,抗湿滑性能提高,滚动阻力和动态生热降低,耐磨性能和抗切割性能较差。
关键词:溶聚丁苯橡胶;乳聚丁苯橡胶;炭黑;白炭黑;胎面胶;动态粘弹性
中图分类号:TQ330.38;TQ333.1文献标志码:A文章编号:1000-890X(2012)02-0084-07
抗湿滑性能、滚动阻力和耐磨性能是乘用轮胎胎面胶的三大重要性能,由于提高这些性能的条件相互制约,同时提高3项性能至今还是对胎面材料发展的一个挑战,因此有人形象地将其称为胎面胶性能的魔法三角[1]。随着应用白炭黑填充溶聚丁苯橡胶(SSBR)制备“绿色轮胎”技术的发展,白炭黑替代炭黑可以改善湿路面刹车止滑性与胎面滚动阻力已成为不争的事实,然而对于这方面的详细机理解释还存在许多不明之处。
本工作采用炭黑和白炭黑分别与SSBR和乳聚丁苯橡胶(ESBR)共混制备4种胶料,从橡胶分子结构、填料在混炼胶中的网络结构、填料-橡胶界面相互作用以及硫化胶动态粘弹特性对SSBR和ESBR胎面胶性能的影响进行综合分析,以期为高性能乘用轮胎配方设计及生产工艺的开发提供参考。
1 实验
1.1 主要原材料
锡偶联SSBR,牌号2305,偶联度为40%,苯乙烯质量分数为0.256,乙烯基质量分数为0.362,数均相对分子质量为252 000,多分散因数为1.75,中国石化北京燕山石油化工股份有限公司产品;ESBR,牌号1502,苯乙烯质量分数为0.228,乙烯基质量分数为0.21,数均相对分子质量为221 800,多分散因数为4~6,中国石油吉林石化公司产品;炭黑N234,卡博特化工(天津)有限公司产品;沉淀法白炭黑,牌号Ultrasil VN3,青岛德固赛化学有限公司产品;偶联剂Si69,南京曙光化工集团有限公司产品。
1.2 试验配方
炭黑和白炭黑以等体积分数填充SBR。试验配方如表1所示。
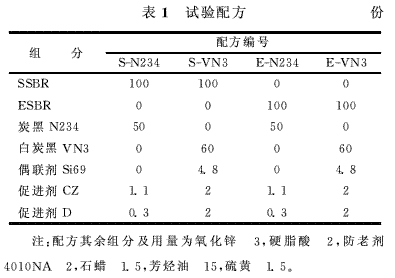
1.3 试样制备
炭黑胎面胶按常规混炼工艺在开炼机上混炼(最后加入芳烃油和硫黄),混炼均匀,出片。白炭黑胎面胶混炼工艺如下:将白炭黑与偶联剂Si69物理混合后,按常规工艺在开炼机上将白炭黑混合物与生胶混合,混合完毕停放1h后,在热辊开炼机上进行热处理[(145~150)℃×7min],而后在开炼机上依次加入其他配合剂,混炼均匀,下片。
混炼胶停放16h后,采用北京环峰化工机械实验厂生产的P3555B2型硫化仪测得t90。混炼胶在平板硫化机上硫化,硫化条件为150℃×t90。
1.4 性能测试
1.4.1 滚动阻力
采用北京万汇一方科技发展有限公司生产的RRS-Ⅱ型橡胶功率损耗试验机进行测试,载荷为30kg,转速为1 200r·min-1,测试时间为90min。
1.4.2 耐磨性能
采用江苏明珠试验机械有限公司生产的MZ-4061型磨耗试验机按GB/T 1689—1998《硫化橡胶耐磨性能的测定(用阿克隆磨耗机)》进行测试。
1.4.3 湿摩擦因数
采用江苏沭阳高速公路仪器有限公司生产的BM-Ⅲ型摆式摩擦因数仪进行测试,摩擦面为毛玻璃(粗糙度为3μm),使用毛刷均匀刷过毛玻璃表面以控制水膜厚度,摆锤滑过毛玻璃距离为126mm,环境温度为25℃。
1.4.4 抗切割性能
采用北京万汇一方科技发展有限公司生产的RCC-Ⅰ型橡胶动态切割试验机进行测试,试样转动速度为720r·min-1,切割频率为120次·min-1,切割时间为20min。
1.4.5 动态力学性能
采用美国阿尔法科技有限公司生产的RPA2000型橡胶加工分析仪(RPA)对生胶进行应变扫描,测试条件为:频率 0.1Hz,温度 100℃,应变范围 0.28%~70%。对生胶进行频率扫描,测试条件为:温度 100℃,应变 14%,频率范围 0.05~32Hz。对混炼胶进行应变扫描,测试条件为:频率 1Hz,温度 100℃,应变范围 0.28%~400%。对硫化胶进行应变扫描,测试条件为:频率 10Hz,温度 60℃,应变范围 0.28%~40%。
采用法国01dB-Metravib公司生产的VA3000型动态力学分析仪(DMA)对硫化胶进行温度扫描,测试条件为:拉伸模式或薄膜双剪切模式,应变 5%,频率 10Hz,温度 -20~+80℃,升温速率 3℃·min-1。其他性能均按相应的国家标准进行测试。
2 结果与讨论
2.1 生胶加工性能
SSBR和ESBR生胶的门尼粘度[ML(1+4)100℃]分别为54和51,SSBR生胶的门尼粘度大于ESBR生胶。
SSBR和ESBR生胶的剪切储能模量(G′)-应变(ε)曲线如图1所示。
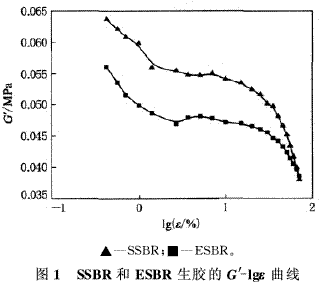
从图1可以看出,SSBR生胶的G′大于ES-BR生胶,这主要是由于SSBR为部分偶联型,偶联度为40%,起到了类似交联点的作用。加工过程中发现SSBR的包辊性不及ESBR,但提高辊温,其包辊性改善。
SSBR和ESBR生胶的损耗因子(tanδ)-频率(f)曲线如图2所示。
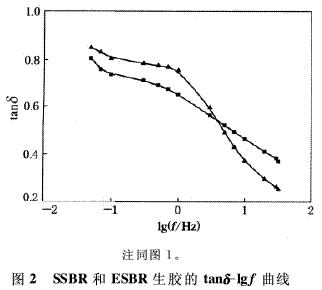
从图2可以看出,与ESBR相比,SSBR对频率具有更高的敏感性。根据时温等效原理,提高温度与降低频率具有同等效果,与ESBR相比,SSBR对加工温度具有更高的敏感性。因此,在SSBR加工过程中需要保持一定辊温,降低胶料粘度,改善加工性能。
2.2 Payne效应与填料网络结构
采用RPA测试SSBR和ESBR混炼胶的G′-lgε曲线,结果如图3所示。
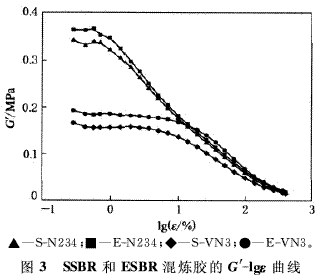
采用炭黑填充时,填料与橡胶相互作用的本质主要是物理作用(物理吸附),而作为偶联剂的双官能硅烷在白炭黑和橡胶之间建立的是化学键[2]。从图3可以看出,与白炭黑填充胶相比,炭黑填充混炼胶的Payne效应高于相同体积分数用偶联剂Si69(用量为白炭黑用量的8%)处理过的白炭黑填充混炼胶,说明混炼胶中炭黑粒子形成的网络结构比白炭黑粒子形成的网络结构强。尽管白炭黑自身与橡胶的相互作用小,但是由于硅烷偶联剂作用产生的共价键使橡胶分子链固定在白炭黑表面,制得混炼胶中白炭黑填料网络较弱,即便在高应变范围内填料-橡胶网络结构也非常稳定。炭黑填料网络结构较强,会在很小的形变下被破坏。
同种填料在SSBR中的网络结构较弱。一方面有文献研究结果表明,拥有较高相对分子质量的橡胶分子会优先与填料形成结合胶,从而减少填料聚集[3];另一方面,由于SSBR与ESBR聚合方法不同,导致SSBR中烃质量分数高达0.99左右,而ESBR中烃质量分数为0.94,其余为有机酸和皂类[4],ESBR中的非烃物质绝大多数为表面活性剂,表面活性剂会很容易地吸附在炭黑或白炭黑的表面,从而降低填料与橡胶分子链的结合。
2.3 硫化特性
SSBR和ESBR胶料的硫化曲线如图4所示。
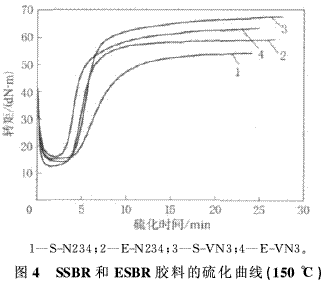
从图4可以看出,白炭黑填充胶的ΔM(MH-ML)大于炭黑填充胶,而通常ΔM可以反映硫化胶的交联密度大小。含硫黄和促进剂的胶料在硫化过程中是通过硫黄桥键交联的,因此硫黄用量以及硫黄与促进剂之比影响交联网络结构。而在白炭黑填充胶中,偶联剂Si69的加入一方面强化了白炭黑与橡胶的界面,同时偶联剂Si69也可参与硫化[5]。正如图4所示,白炭黑填充胶的ΔM大于炭黑填充胶。
采用相同填料填充SBR时,白炭黑填充SS-BR胶料比其填充ESBR具有更大的ΔM,说明加入偶联剂Si69后白炭黑与SSBR具有更强的橡胶-填料相互作用。G.Heinrich等[6]提出SSBR和ESBR与沉淀法白炭黑相互作用模型,白炭黑的结构中存在孔洞,活动性较强的橡胶分子链可以进入孔洞。SSBR具有部分直链结构,而ESBR存在较多支链,因此SSBR比ESBR更容易进入白炭黑结构的孔洞中。以前的工作[7]通过核磁交联密度仪测试SBR生胶和白炭黑结合橡胶的1 H-NMR弛豫参数T2,研究得出SSBR与白炭黑具有更强的界面作用,形成的结合橡胶层更厚,分子链运动受限程度更大。而在炭黑填充两种SBR中,由于SSBR的乙烯基结构质量分数较高(SS-BR乙烯基质量分数为0.362,ESBR乙烯基质量分数为0.21)[4],主链双键浓度相对较低,一方面使SSBR的起硫时间延长,另一方面导致其分子间交联密度下降。
2.4 物理性能
炭黑与白炭黑填充SSBR和ESBR硫化胶物理性能如表2所示。
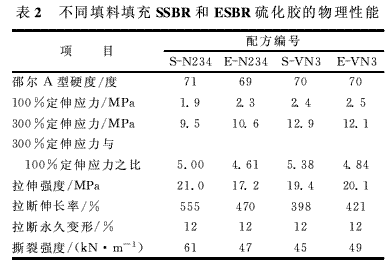
从表2可以看出,与硫化曲线的转矩相一致,由于偶联剂Si69的加入,白炭黑填充SBR硫化胶的300%定伸应力大于炭黑填充胶,拉断伸长率比炭黑填充胶小。对比炭黑填充的两种SBR,ESBR硫化胶的定伸应力较高。
2.5 抗湿滑性能和耐磨性能及滚动阻力SSBR和ESBR硫化胶的抗湿滑性能和耐磨性能及滚动阻力如表3所示。
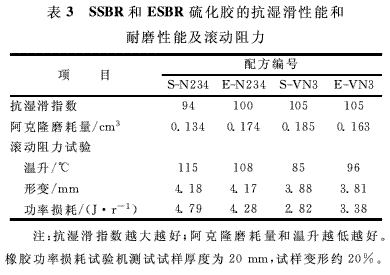
从表3可以看出,抗湿滑指数以炭黑填充ESBR作为基准,白炭黑填充SBR硫化胶的抗湿滑指数增大了5%,S-N234硫化胶的抗湿滑指数减小了6%。由于在橡胶与路面之间存在水的作用,王梦蛟[8-9]认为白炭黑填充硫化胶试样的摩擦表面有刚性白炭黑粒子裸露,在微观上起到刺破水膜作用,从而提高硫化胶的抗湿滑性能。由于微观粗糙度的存在,通过刺破水膜从而增大胎面胶与路面的实际接触面积可能是白炭黑填充胶拥有较高抗湿滑性能的一个重要原因。
S-N234硫化胶的阿克隆磨耗量最小,这主要是由于锡偶联SSBR在填充炭黑的混炼过程中,强剪切作用伴随着弱锡-碳键的破坏,炭黑自动向大分子链转移,炭黑吸附橡胶分子链的作用大大弥补了SSBR由于高剪切作用而引起的相对分子质量减小,起到了“锡偶联”作用。而ESBR合成过程中残留的皂类物质包覆在炭黑表面,大大降低了炭黑的表面活性,同时降低了填料与橡胶之间的相互作用,从而使炭黑填充ESBR的耐磨性能较其填充SSBR差。
炭黑与白炭黑填充SBR硫化胶的阿克隆磨耗表面形貌如图5所示。
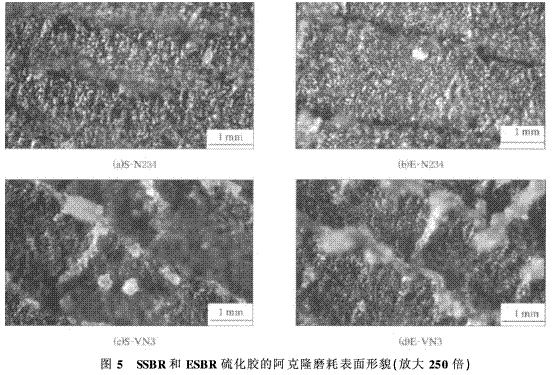
从图5可以明显看出炭黑与白炭黑填充SBR磨耗表面形貌的不同。阿克隆磨耗过程并没有在硫化胶表面形成沙马赫图纹(1952年沙马赫进行的有关橡胶磨损方面开拓性的工作表明,在平滑磨耗试验中产生的磨耗图纹与所施加的摩擦应力垂直。这一橡胶磨损的独特形貌被规定为沙马赫图纹),而是形成了与磨耗轮运行方向成一定角度的磨耗图纹。相比炭黑填充的硫化胶,白炭黑填充的硫化胶磨耗图纹与运行方向的夹角更大。
采用橡胶功率损耗试验机测试的SSBR和ESBR硫化胶的温度-时间曲线和功率损耗-时间曲线分别如图6和7所示。从图7可以看出,在4种胶料硬度基本一致的前提下,白炭黑填充硫化胶的功率损耗远低于炭黑填充硫化胶。由于采用炭黑填充时,填料与橡胶之间主要是物理作用,炭黑会在胶料受力的过程中局部产生分子滑移,滑动内摩擦使胶料产生滞后损失,并以热量的形式消耗。目前比较认可的影响滚动阻力的因素是填料网络的强弱,在动态形变下,填料网络遭到破坏,损耗主要来源于填料粒子间的相互摩擦作用和因填料网络破坏后释放的橡胶部分变形[10],因此填料网络的破坏与重建是动态应变下能量耗散的主要原因。
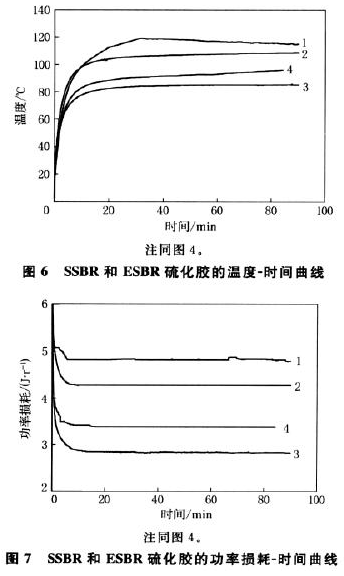
与此同时,有经验表明,当轮胎沿路面滚动时,每转一圈就会承受一次变形,这种变形产生的能量(即滞后损失)以热能形式被耗散,即为滚动阻力。其频率在10~100Hz范围内,这取决于轮胎的滚动速度,正常行驶时轮胎内的散热(温升)达50~80℃,因此一般选择10Hz,60℃条件下胶料的tanδ值作为胎面胶滚动阻力的评判标准[11]。
SSBR和ESBR硫化胶的tanδ-lgε曲线如图8所示,采用RPA对SSBR和ESBR硫化胶进行应变扫描,当应变为20%时,功率损耗与tanδ(60℃)之间的相关性如图9如示。
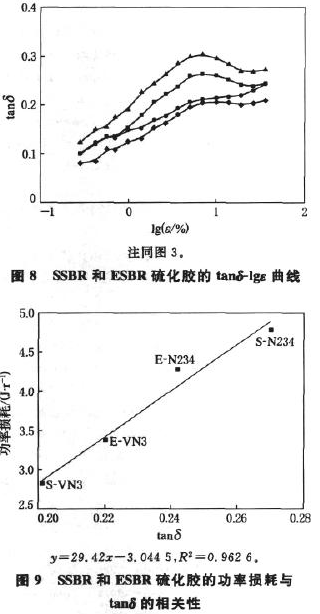
从图8和9可以看出,功率损耗与tanδ之间有很好的线性相关性。
2.6 抗切割性能
动态切割试验用来表征轮胎在非常苛刻的路面(如有尖锐石子凸起的野外路面)上的抗破坏能力。有文献认为硫化胶的机械强度、抗裂纹增长能力与抗切割性能正相关[12]。由于抗切割过程也是一个能量吸收过程,因此较高滞后的胶料将拥有较好的抗切割能力[13]。
S-N234,E-N234,S-VN3和E-VN3硫化胶的切割量分别为0.74,2.01,3.60和2.05g。可以看出,炭黑填充SBR硫化胶的抗切割能力优于相应白炭黑填充的SBR硫化胶。
2.7 橡胶材料的粘弹性与抗湿滑性能和滚动阻力的关系
橡胶作为典型的粘弹性材料,其模量、强度等性能具有很强的温度、频率依赖性,尤其是采用纳米填料补强的橡胶复合材料还具有很强的应变依赖性,这就决定了胎面胶的以上各项物理性能均可能与橡胶复合材料的本身粘弹性有关。有文献提出,由于橡胶的摩擦力及滚动阻力通过橡胶材料周期形变影响到能量损耗,因此使用变形指数的解析方法能够得到各温度范围内的粘弹性与轮胎性能的关系。其中-10~+10℃下的tanδ值较大的胶料具有更好的抗湿滑性能,而50~70℃下tanδ值较小的胶料具有更低的滚动阻力。采用DMA对SBR硫化胶进行温度扫描,以期得到动态粘弹性与抗湿滑性能和滚动阻力的关系,试验结果如图10和11所示。
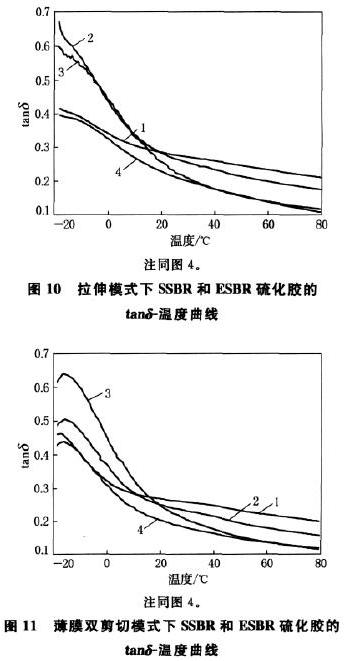
从图10和11可以看出,对于炭黑填充胶,无论采用何种应变模式,0℃下的tanδ值均能很好地反映其抗湿滑性能的差异,而在白炭黑填充胶中DMA与摆锤摩擦因数仪测得的抗湿滑指数结果并不吻合。同时DMA测得的白炭黑填充胶在60℃下的tanδ值也没有如RPA测试结果那样很好地反映出滚动阻力的差别,这说明测试模式和应变范围的选择对测试结果影响很大。因此选择合理的测试模式以及应变振幅是获得可靠数据的前提。
3 结论
(1)采用不同填料填充SBR制备的硫化胶在使用性能上各有优劣。白炭黑填充SSBR硫化胶在提高抗湿滑性能和降低滚动阻力两方面表现突出,而炭黑填充SSBR硫化胶拥有较好的耐磨性能和抗切割性能。
(2)动态条件下填料与橡胶相互作用产生的滞后生热是滚动阻力的直接来源,采用RPA获得的10Hz,60℃下的tanδ值可以很好地反映硫化胶的滚动阻力。而在有水参与的复杂摩擦体系下,仅仅用-10~+10℃下的tanδ值来表征与橡胶高频形变有关的抗湿滑性能是不够全面的。
参考文献:略