倪露萍,许海燕,吴驰飞(华东理工大学材料科学与工程学院,上海 200237)
摘要:研究混炼工艺对丁苯橡胶(SBR)/顺丁橡胶(BR)/白炭黑胶料物理性能和结合胶含量的影响。对于一次投胶混炼法,橡胶对白炭黑的润湿效果好,胶料的拉伸强度和结合胶含量大于分段投胶混炼法胶料。对于分段投胶混炼法,用贫相橡胶控制结合胶时,胶料的拉伸强度和结合胶含量较大;结合胶含量受生胶种类和并用比以及混炼工艺的共同影响;2种生胶的用量越接近,越容易形成结合胶,形成结合胶的白炭黑表面越大;混炼工艺引起的混炼场差异影响结合胶的生成。
关键词:混炼工艺;顺丁橡胶;丁苯橡胶;白炭黑;结合胶;物理性能
近年来,为降低轮胎的滚动阻力,白炭黑在轮胎胶料中的应用研究深受重视。本工作探讨混炼工艺对丁苯橡胶(SBR)/顺丁橡胶(BR)/白炭黑胶料物理性能和结合胶含量的影响。
1 实验
1.1 原材料
丁苯橡胶(SBR),牌号Nipol SBR1502,结合苯乙烯含量23.5%,日本瑞翁公司产品;顺丁橡胶(BR),牌号Ubepol BR130B,顺式-1,4结构含量96%,日本宇部兴产公司产品;白炭黑UltrasilVN3GR和偶联剂Si266,德国德固赛公司产品;操作油NH-60,日本出光兴产公司产品;促进剂CZ、促进剂D、硫黄、氧化锌、硬脂酸和防老剂4020,江阴海达橡塑制品有限公司提供;甲苯,分析纯,上海凌峰化学试剂有限公司产品。
1.2 主要仪器与设备
哈克转矩流变仪,德国赛默飞世尔科技有限公司产品;WSM-20KN型拉力机,长春智能试验机研究所产品。
1.3 胶料配方
胶料配方见表1。
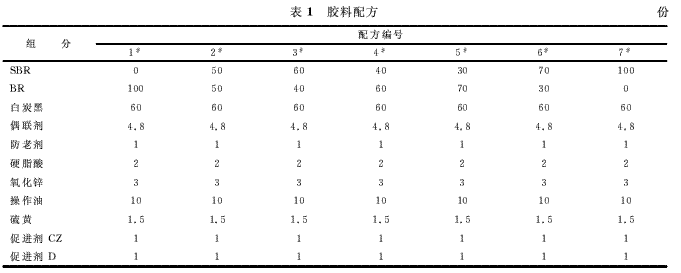
1.4 混炼工艺
胶料混炼在哈克转矩流变仪中进行,密炼室填充因数为0.7,转子转速为60r·min-1,混炼温度设定为125℃。采用2种方法进行混炼。
(1)一次投胶混炼法。该法的一段混炼胶由全部生胶、白炭黑、偶联剂和白炭黑、1/2小料混炼制成;二段混炼胶由一段混炼胶与剩余1/2小料混炼制成。本研究中一次投胶混炼法简称为一步法。
(2)分段投胶混炼法。该法可以达到控制结合胶的目的,所以又称结合胶控制方法。一段混炼胶由一种生胶、白炭黑和偶联剂、1/2小料混炼制成;二段混炼与一段混炼的密炼室填充量相同,二段混炼胶由一段混炼胶、另一种生胶、剩余1/2小料混炼制成。其中一段混炼投入的生胶称为结合胶控制用胶,若其含量超过生胶总量的1/2,则称为富相控制,反之称为贫相控制。本研究中SBR与白炭黑先混炼的分段投胶混炼法简称为SBR先混法;BR与白炭黑先混炼的分段投胶混炼法简称为BR先混法。
1.5 性能测试
(1)胶料物理性能测试按相应国家标准进行。
(2)结合胶含量测试。混炼胶在室温下停放1个星期,进行抽滤试验:准确称取1g混炼胶,用滤纸包好,浸泡于200mL甲苯溶剂中,在30℃下恒温浸泡45h后取出,通风干燥24h至恒质量。结合胶含量由下式计算。
φB=(m2-m1×φ2)/(m1×φ1)。
式中,φB为结合胶含量;m1和m2分别为混炼胶抽滤前后的质量,φ1和φ2分别为混炼胶中橡胶和炭黑含量。
2 结果与讨论
2.1 物理性能
不同混炼工艺制备的SBR/BR/白炭黑胶料物理性能如表2所示。
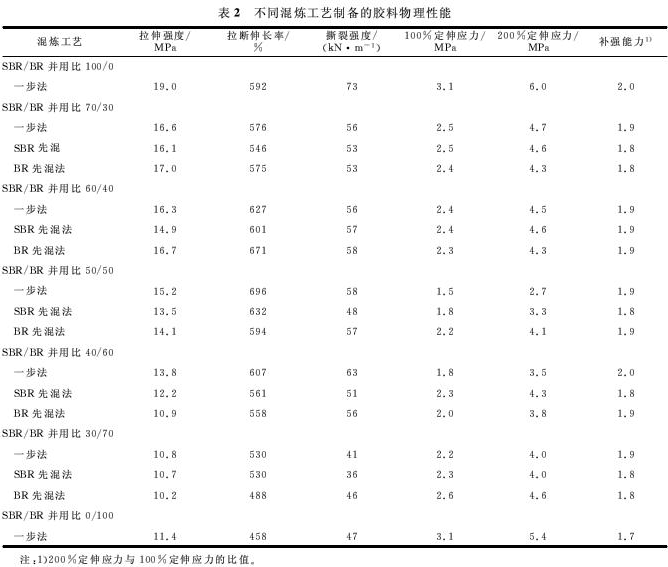
从表2可以看出混炼工艺对胶料拉伸强度的影响。对于SBR/BR并用比相同而混炼工艺不同的胶料,结合胶不同,拉伸强度不同。在橡胶的混炼过程中,白炭黑(填料)在橡胶基体中的分散主要为白炭黑的润湿和团聚体破裂。一步法胶料的白炭黑润湿效果好,其拉伸强度总体大于分段投胶混炼法胶料。
进一步分析得出,当贫相橡胶控制结合胶时,胶料的拉伸强度高于富相橡胶控制结合胶的胶料,这说明一段混炼中白炭黑与橡胶的用量比显著影响胶料的物理性能。对于分段投胶混炼法,一段混炼中加入的橡胶量比一步法小,橡胶对白炭黑的润湿变差,此时白炭黑与橡胶的结合也随之变差。当贫相橡胶控制结合胶时,一段混炼中橡胶投入量小,即降低了白炭黑的不良分散程度,从而有利于提高胶料的拉伸强度。结合胶成分对胶料拉伸强度影响不是很大,但与控制结合胶的橡胶用量引起的密炼室混炼条件变化相关。
从表2还可以看出,BR先混法胶料的抗撕裂性能比SBR先混法胶料好。这说明结合胶成分对胶料抗撕裂性能影响较明显,分子链运动性较好的BR可以得到更好的相界面结合效果。
2.2 结合胶含量
不同混炼工艺制备的SBR/BR/白炭黑胶料结合胶含量见表3。结合胶是实现补强性能的基本要素[1]。
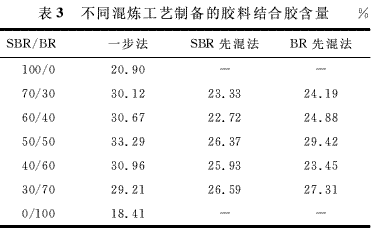
从表3可以看出,一步法胶料的结合胶含量较大,拉伸强度较大;分段投胶混炼法胶料贫相橡胶控制的结合胶含量总体较大。这是因为结合胶一旦形成就很难剥离,而结合胶表面也不易再包覆异种橡胶[2],因此贫相橡胶控制结合胶时,由于一段混炼中橡胶投入量小,即降低了白炭黑的不良分散程度,有利于二段混炼时结合胶形成,增大了胶料整体的结合胶含量。
当SBR/BR并用比为50/50时,胶料结合胶含量较大,说明生胶并用比会影响胶料的混炼效果,在2种生胶用量均衡的条件下更容易生成结合胶;BR先混的胶料结合胶含量大于SBR先混的胶料,说明BR与白炭黑的结合效果更好,这与BR优良的润湿性能有关。SBR/BR/白黑胶料结合胶含量与拉伸强度的关系如图1所示。
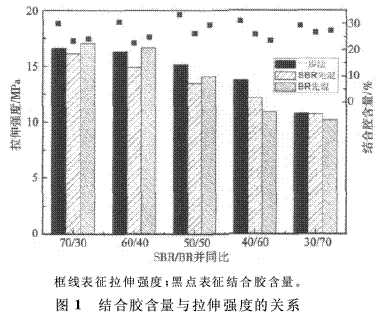
从图1可以看出,结合胶含量变化趋势与拉伸强度变化趋势基本相同,说明结合胶含量与拉伸性能之间是存在一定关系;但控制结合胶的胶料与未控制结合胶的胶料拉伸强度与结合胶含量之间的关系并不完全一致。比较3种混炼工艺胶料发现,不同混炼工艺制备的胶料表现出不同的性能变化规律。这说明结合胶含量以及基体橡胶对胶料的拉伸性能并不是仅有的决定因素。
不同混炼工艺引起的橡胶基体形态上的变化也可能影响胶料的拉伸性能,胶料的各种界面结合情况对其物理性能的影响是重大的。作为白炭黑-橡胶界面的结合胶,其外层分子链的柔顺性以及与之相接触并结合的基体橡胶分子链的柔顺性是决定其效能的关键因素。尤其结合胶的分子链,当其具有一定的柔顺性时可与基体橡胶分子链形成强有力的缠结和相互渗透,从而形成牢固且厚的界面,与基体良好相容且稳定。本研究中白炭黑-橡胶界面在两相橡胶界面的形成中起到很重要的作用。白炭黑就像两相橡胶的相容剂一样,通过结合胶形成较强、较稳定的两相结合[3],而在某种程度白炭黑作为物理交联点起稳定工艺和补强的作用[4]。因此对于这个体系来说,基体橡胶、结合胶以及共混体系形态共同影响胶料的拉伸性能。
3 结论
(1)对于SBR/BR/白黑胶料,一步法胶料的拉伸强度和结合胶含量比分段投胶混炼法胶料大,这在于一步法胶料的白炭黑润湿效果好。
(2)在分段投胶混炼中,当贫相橡胶控制结合胶时,胶料的拉伸强度较高,这在于一段混炼时生胶的投入量较小,白炭黑在基体中的整体分散和结合效果较好;作为补强基本要素的结合胶含量越大,越有利于提高胶料的强度。
(3)结合胶含量受生胶种类和并用比以及混炼工艺的共同影响。2种生胶的用量越接近,越容易形成结合胶;分子链柔顺性越好,对白炭黑的润湿效果越好,形成结合胶的白炭黑表面越大;混炼工艺引起的混炼场差异影响结合胶的生成。
(4)基体橡胶、结合胶以及共混体系形态共同影响胶料的拉伸性能。
参考文献:略