肖建斌(青岛科技大学橡塑材料与工程教育部重点实验室,山东青岛 266042)
摘要:用断裂力学方法研究炭黑N110,N220和N330补强NR硫化胶的疲劳破坏特性。结果表明,随着疲劳时间的延长,3种炭黑补强硫化胶的拉断形变能密度均减小,且炭黑粒径越小,硫化胶的拉断形变能密度降幅越大;炭黑粒径越小的硫化胶内部潜在缺陷越小,但抗裂纹扩展性能越差,疲劳寿命越短;3种炭黑补强硫化胶的疲劳寿命方程均能较准确地预测其疲劳寿命。
关键词:NR;炭黑;动态疲劳;疲劳破坏;疲劳寿命;断裂力学
中图分类号:TQ332;TQ330·38+1;TQ330·7文献标识码:A文章编号:1000-890X(2006)01-0016-04
按照断裂力学的观点,疲劳破坏是指在疲劳过程中由于应力集中,材料的潜在缺陷产生微量增长而形成裂纹,裂纹再逐渐扩展直至材料断裂的现象[1]。
橡胶材料的疲劳破坏特性不仅取决于胶料配方和疲劳破坏条件,而且取决于动态变形过程中橡胶材料的微观结构和物理性能变化[2]。研究橡胶材料的疲劳破坏特性,对保证橡胶制品使用的安全性和可靠性具有重要的意义。
评价疲劳破坏特性最可靠的方法是进行实际使用条件下的测试,但这需要较长的时间和昂贵的费用。因此,一般是在特定条件下对材料进行拉伸或压缩等动态试验,并绘制出疲劳寿命曲线,从而获得材料的疲劳破坏特性。
1 实验
1·1 原材料
NR,1#标准胶,海南农垦橡胶总公司产品;炭黑N110,N220和N330,青岛德固萨化学有限公司产品;其它配合剂均为市售工业品。
1·2 试验配方
NR 100,炭黑(变品种) 50,氧化锌 5,硬脂酸 3,硫黄 2·25,促进剂DM 1,防老剂4010NA 1·5,石蜡 1。
1·3 试样制备
胶料按常规工艺混炼,在50 t平板硫化机上硫化,硫化条件为145℃/10
MPa×t90。将硫化胶片裁成哑铃形试样(裁刀狭长部分的宽度为10mm),部分试样用自制刀具切出锐利的单边切口,切口深度用读数显微镜测试。
1·4 测试
(1)拉伸疲劳破坏试验按GB/T 1688—1986在PL-140型拉伸疲劳试验机(上海化工机械四厂产品)上进行,拉伸频率为500
r·min-1。
(2)试样断面形貌采用JEM-2000型扫描电子显微镜(SEM)观察,观察前对试样断面作真空喷金处理,镀金膜厚度为0·02μm。
2 结果与讨论
2·1 动态疲劳破坏历程
唯象论认为,材料的疲劳破坏是由于其内部缺陷(气泡、微裂纹等)引发的裂纹不断传播和扩展导致的。裂纹的传播方式和扩展速度由材料的粘弹性决定,表现出强烈的时间-温度效应。
分子论观点认为,橡胶材料的动态疲劳破坏归因于化学键的断裂,即试样在周期性应变过程中,应力不断集中于橡胶分子网链“弱”键处而产生微裂纹,微裂纹处的分子网链继续断裂而形成宏观裂纹,直至材料破裂。裂纹发展是分子网链连续断裂的粘弹性非平衡过程[3,4],该过程包括随时间延长分子网链连续不可逆断裂以及裂纹尖端处和其附近与分子运动有关的塑性变形。分子网链的断裂能以热的形式散发掉,这一微观过程的宏观表现是动态疲劳过程中裂纹穿过试样不断扩展,直至试样断裂。
疲劳裂纹增长是机械作用和化学反应累积到一定程度产生的,即疲劳过程中各种物理和化学因素共同作用导致分子网链断裂以及加速材料的疲劳老化过程。
动态疲劳过程大致分3个阶段:第1阶段,应力发生急剧变化,出现应力软化现象;第2阶段,应力变化缓慢,材料表面或内部产生损伤(破坏核);第3阶段,损伤引发裂纹并连续扩展,直至断裂破坏,这是材料疲劳破坏的关键阶段。
2.2 疲劳破坏特性
2·2·1 拉断形变能密度
拉断形变能密度反映硫化胶的抗拉断性能,拉断形变能密度大,硫化胶的抗拉断性能好[5]。硫化胶的拉断形变能密度的测试方法是:先将试样进行一定时间的拉伸疲劳试验,再将试样在电子拉力机上拉伸至断裂并测得应力-应变曲线,对曲线下的面积积分即得试样的拉断形变能密度。3种炭黑补强硫化胶拉断形变能密度与疲劳时间的关系如图1所示[拉伸比(λ)为1·5]。
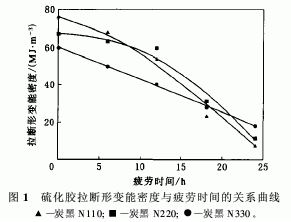
从图1可以看出,在疲劳试验的初始阶段,炭黑N110补强硫化胶的拉断形变能密度最大,炭黑N220补强硫化胶次之,炭黑N330补强硫化胶最小;随着疲劳时间的延长,3种炭黑补强硫化胶的拉断形变能密度均减小,炭黑N110补强硫化胶的拉断形变能密度降幅最大,炭黑N220补强硫化胶次之,炭黑N330补强硫化胶最小。其原因是,在疲劳过程中,由于机械作用和化学反应导致橡胶交联网络变化,即机械作用引起的橡胶分子链断裂以及氧和臭氧老化等反应引起的橡胶分子降解和交联致使交联网络中形成较多的链端,使得硫化胶的耐疲劳破坏性能降低;粒径小、比表面积大的炭黑对橡胶分子的吸附力大,使得承受应力的橡胶链段不能很快地通过分子运动产生应力松弛,致使橡胶分子链中的化学键在应力的作用下被减弱或打断;另外,粒径小、比表面积大的炭黑提高了硫化胶疲劳过程中的内耗,使硫化胶疲劳温升提高,橡胶分子氧化降解速度加快,导致硫化胶的强度和耐疲劳破坏性能降低[6]。
2·2·2 疲劳寿命
(1)疲劳寿命曲线
疲劳寿命曲线也称S-N曲线,S代表拉伸比、应力或应变,N为疲劳寿命。3种炭黑补强硫化胶的S-N曲线如图2所示。
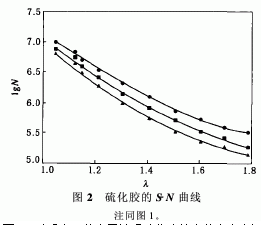
从图2可以看出,3种炭黑补强硫化胶的疲劳寿命由短到长的顺序为炭黑N110,
N220,N330。出现这一现象的原因是橡胶分子之间和橡胶分子与炭黑之间过强的相互作用会限制能量耗散所需的分子运动,即粒径小、比表面积大的炭黑对橡胶变形(分子运动)阻碍大,其补强硫化胶的往复变形内耗大、温升高,热氧、臭氧老化等反应强烈,耐疲劳破坏性能差。
(2)疲劳寿命方程
用数学模型lgN=a+b1λ+b2λ2对炭黑补强硫化胶的S-N曲线进行拟合[7],采用回归分析法求出a,b1和b2,得出炭黑N110补强硫化胶的疲劳寿命方程及复相关因数(R2)为:
lgN=15.075-9.265 1λ+2.153 7λ2
R2=0·997 7
炭黑N220补强硫化胶的疲劳寿命方程及复相关因数为:
lgN=13.427-7.117λ+1.519 3λ2
R2=0·997 8
炭黑N110补强硫化胶的疲劳寿命方程及复相关因数为:
lgN=13.306-6.908 7λ+1.500 2λ2
R2=0·998 8
可以看出,3种炭黑补强硫化胶的疲劳寿命方程的相关因数均接近于1,即各方程均可较好地拟合硫化胶的S-N曲线,较准确地预测硫化胶的疲劳寿命。
2·3 疲劳断裂特征
(1)参数β和C0
β和C0通过S-N曲线(采用伤痕长度与疲劳寿命叠加法[8],将图2曲线向较小拉伸比方向延伸)求出,可以定量表征硫化胶的疲劳断裂特性[9]。β值与S-N曲线的形状有关,β值越大,表明随着拉伸比增大,硫化胶的裂纹扩展速度越快;C0表征硫化胶中潜在缺陷的等价微裂纹尺寸,C0值越大,硫化胶中潜在缺陷的尺寸越大。试验测得的3种炭黑补强硫化胶的β和C0值见表1。
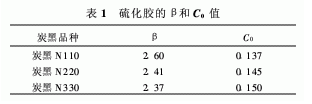
从表1可以看出,炭黑N110补强硫化胶的β值最大,C0值最小,说明炭黑N110补强硫化胶的潜在缺陷最小,但裂纹扩展速度最快;炭黑N330补强硫化胶的β值最小,C0值最大,说明炭黑N330补强硫化胶裂纹扩展速度最慢,但潜在缺陷最大;炭黑N220补强硫化胶的β值和C0值居中,说明炭黑N220补强硫化胶的潜在缺陷和裂纹扩展速度居中。
(2)断面形貌
3种炭黑补强硫化胶断面形貌如图3~5所示。
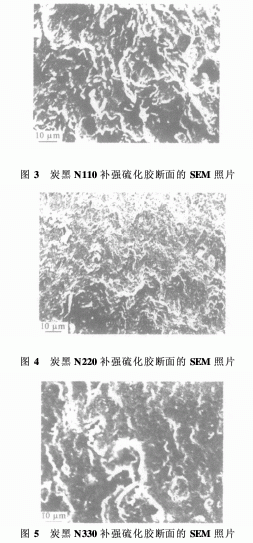
从图3~5可以看出,炭黑N110补强硫化胶的断面较平整、光滑,孔洞最小,呈脆性断裂形貌,说明炭黑N110补强硫化胶的潜在缺陷最小,但裂纹扩展速度快;炭黑N220补强硫化胶的断面裂纹清晰,孔洞较大,说明炭黑N220补强硫化胶的潜在缺陷较大;炭黑N330补强硫化胶的断面凹凸不平,孔洞最大,呈延展性破坏形貌,说明炭黑N330补强硫化胶的裂纹扩展速度慢,但潜在缺陷最大。该结论与前面的结论吻合。
3 结论
(1)随着疲劳时间的延长,炭黑N110,N220和N330补强NR硫化胶的拉断形变能密度均减小,且炭黑粒径越小,硫化胶的拉断形变能密度减小越快。
(2)炭黑粒径越小的NR硫化胶内部潜在缺陷越小,但裂纹扩展速度越快,疲劳寿命越短。(3)3种炭黑补强NR硫化胶的疲劳寿命方程能较准确地预测其疲劳寿命。