汪传生,祝卫国(青岛科技大学,山东青岛 266042)
作者简介:汪传生(1960-),男,安徽安庆人,青岛科技大学教授,博士,主要从事高分子材料加工技术、装备及机电一体化的教学和科研工作。
要提高橡胶制品的加工质量以及更好地利用原料和能源,必须重视胶料的混炼。在分析混炼工艺以及研究和评价混炼设备性能时,混炼胶的质量是重要的衡量标准之一。在通常的操作条件下,一般是通过测定混炼胶的密度和硫化曲线,或测定硬度和定伸应力来评价混炼胶质量。这些评价方法只是根据混炼胶性能间接衡量其质量,会受到原料性质的波动、配合剂计量的误差等与实际混炼工艺和设备无关的因素的影响。
混炼胶的质量与炭黑粒子分布的均匀性有关,已经证实在胶料耐磨性与填充剂分散度之间存在着一定的相关性[1]。炭黑在混炼胶中的分散度是直接衡量胶料混炼质量及评价混炼设备性能的标准[2],因此对炭黑分散度的测定应给予特别重视。
1 胶料混炼
胶料混炼的主要目的是使胶料中各种填充剂实体尺寸尽量减小及填充剂实体间分布均匀,前者决定性能改善程度,而后者决定性能的均匀程度[3]。胶料中填充剂的分散性可以定义为填充剂实体的尺寸分布(强度因子)和实体间的距离分布(展度因子)。由于橡胶工业最广泛使用的填料是炭黑,因此,主要考察炭黑粒子的大小在混炼过程中的变化。
按帕尔默格伦对混炼过程的分析,5个阶段中的分散和分布混炼起着至关重要的作用[4,5]。分散混炼是将各混炼成分,特别是炭黑的粒径减至最小的混炼作用过程;分布混炼则是在整个加工过程中将各混炼成分完全分开使其均匀化的混炼作用过程。混炼胶的性能不仅与炭黑的分散情况有关,而且与其分布情况有关[6,7]。因此,评价混炼效果应该从分散和分布两个方面综合进行。分散和分布混炼的4种典型效果见图1。
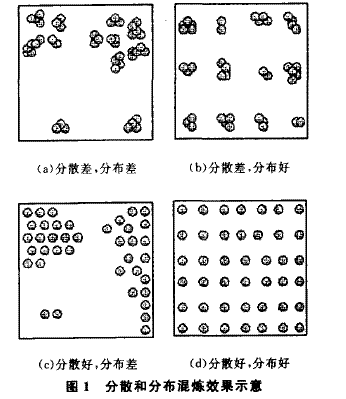
2 炭黑分散度的测定方法
2·1 间接测定法
无论是根据未硫化胶物理性能进行判断的估算法(如测量门尼粘度、挤出收缩率)还是电阻法(如采用数字静电计、韦斯顿式785试验机),都是根据混炼胶的性能来估算炭黑分散度。然而,胶料的物理性能相同,其混炼情况却不一定相同,因此这种方法测定的分散度不能用于准确地评价混炼效果。
2·2 直接测定法
直接测定法主要包括表面观察法、粒径测量法、表面粗造度分析法和改进的显微照相法。
2·2·1 表面观察法
虽然目视观察法、ASTM D 2663A法、R-S法以及GB
6030—1985(显微照相法)存在很多缺点,但有一个优点是肯定的,即训练有素的操作人员能够根据观察到或拍摄到的图像判断胶料中炭黑的分散度。操作人员的判断标准可以综合分散、分布、配方以及混炼操作的具体情况等众多因素。将这些因素分别用数学语言加以表述,并综合成一个分散度判断模型,并可以此改进分散度自动测量装置,相当于建立一个“分散度测量专家系统”。
2·2·2 粒径直接测量法
ASTM D
2663B法(可称为“透射显微镜法”)和扫描式电子显微镜法虽然测量的手段不同,但其所测量的都是胶料中未分散颗粒的大小和数量,即其测量值只是对分散混炼情况的表述,而未涉及分布情况。
2·2·3 表面粗糙度分析法
触针法(ASTM D
2663C法)和光学法(暗视场反射光学显微镜法)测量得到的图像能够直观地反映胶料表面的情况,既能反映分散(峰高、峰值数)又能反映分布(波峰的分布)情况。但最后的测定值却只考虑了峰高和峰值数的平均值,因此只反映了分散情况。
2·2·4 改进的显微照相法
瑞典Optigrader公司的Dispergrader法是一种能够自动判别胶料中炭黑分散度的方法,其原理也是显微照相法。但使用中发现,该仪器对同一胶料的多次重复测试会判定出不同的分散等级。该法判别标准采用菲力浦10级标准,适用性较差。它单纯以图像上白色亮点的个数和面积来判定炭黑的分散度等级,忽略了胶料中浅色配合剂颗粒及胶料表面反光极弱的凹点部分的影响,存在对三段混炼胶料炭黑分散度等级判断不准确的现象[9]。例如,试样原始图像中有气孔,如图2(a)所示,而用该仪器作二进制图像转换后的图片如图2(b)所示,显示为炭黑团大粒子,最后Dispergrader法定为3.2级,使级别偏低;又如试样原始图像中有较大凸起颗粒,如图3(a)所示,而用该仪器作二进制图像转换后的图片如图3(b)所示,大颗粒未显示出来,最后Dispergrader法定为6.8级,使级别偏高。在Dispergrader法的实际操作中,上述试样只能靠人工剔除,因此对人的依赖性较大。
国内研究者在炭黑分散度测定方面也做了大量工作[8,1014],创立的分散度鉴定方法虽然也是以显微照相法为基础,但引入了图像处理技术,能合理确定原始图像转换为二进制图像时的阈值,对某些图片进行切割,以除去图片中气孔、气泡及杂质等。度量标准计算考虑了颗粒的直径和面积,但在计算模型中主要以颗粒的数量和面积来计算。有的计算模型在初期引入了较少的分布信息,但是随着计算的深入,这些信息逐渐退化[8]。
3 存在的问题
综合以上分析,目前胶料中炭黑分散度测定方法主要存在以下问题。
(1)各种测定方法得出的结果均不能综合反映分散及分布水平,这也是造成测定结果不稳定的原因之一。
(2)显微照相改进法中引入的图像处理不充分,使后续计算结果出现较大偏差。
(3)测定标准固定,不能根据胶料配方及混炼工艺的改变做出相应调整。在混炼设备研制与评价中引入错误信息。
(4)评价模型的信息量小,不能充分反映获取图片所携带的信息。
4 改进方案
针对以上分析,提出如下改进途径。

(1)显微照相法(包括改进显微照相法)是一种综合测量分散及分布效果的有效方法,对显微照相法进行改进是改善分散度测定方法的方向。可以通过建立数学模型计算的方法对其进行改进。要提高设备的自动化程度,就必须降低设备对人的依赖程度。因此新型的分散度测定方法应该进一步降低对操作员和试样制作的要求。
(2)运用显微照相法时,应采用彩色摄影来获取彩色图像,这样可以对采用染色处理的试样(如研究橡塑共混的试样)进行测定,扩大仪器的适用范围。
(3)显微照相法获取的图像在分析和测定取值前必须进行图像处理。因为在试样的制作过程中会不可避免地引入一些瑕疵,如刀痕、空穴等。对图像进一步处理可以降低分散度测定对操作者的依赖性。
(4)在对图像进行二进制图像转换前也必须进行处理,例如,进行去背景、去噪声、调节对比度等操作。混炼胶试样的表面放大图像如图4所示。处理时应特别注意阈值的确定,不适当的阈值将会直接影响测定结果(如图5所示)。
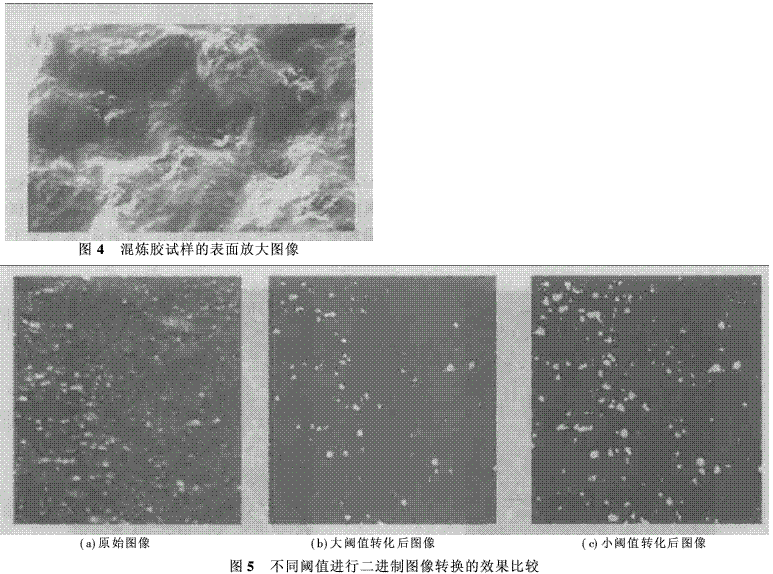
(5)计算模型中应包含“分布因子”。在相同分散情况下,分布情况可能大不相同(见图1)。因此判定分散度时应将混炼胶的分布情况计算在
内,引入“分布因子”或在测定分散指数外再给出分布指数。
(6)借鉴LM分散度计算法的原理,分散度等级的标准应在国家标准的基础上设置新的计算标准。计算标准应包含混炼胶配方信息、混炼工艺信息等。这样既能够保证遵循国家标准的基本信息,又能根据生产实际情况灵活多变。
5 结语
混炼胶中炭黑分散度的测定过程是一个信息的获取过程,也就是从图像(信宿)繁杂零乱的原始信息中提取我们所关心的信息,以揭示炭黑分散的本质和规律。对原始信息应该进行分门别类、归纳演绎、分析综合等一系列的加工处理,才能使其中包含的有效信息显露出来,从而找出其必然联系,使炭黑分散度真正成为衡量混炼效果的标准。
参考文献:
[1]ИСЮряовндр.炭黑分散度对轮胎胶料质量的影响[J].唐云峰译.轮胎工业,1996,16(2):90-92.
[2]黄祖长.NR/BR/EPDM共混胎侧胶中EPDM的结构:分子结构和炭黑分布对性能的影响[J].橡胶参考资料,2001,31(2):29-34.
[3]戴近禹.天然橡胶/顺丁橡胶并用比及炭黑分布对硫化胶性能的影响[J].橡胶工业,1990,37(4):203-210.
[4] Pokluda I.混炼胶中配合剂分散度的评价方法[J].颜 丹译.世界橡胶工业,1990,17(3):81-87.
[5]周彦豪.聚合物加工流变学基础[M].西安:西安交通大学出版社,1988.
[6] Manas Z.Analysis of mixing in polymer processing equipment[J].Rheology
Bulletin,1997,66(1):5-8.
[7]卡·盖克,斯·沙曼.混炼术语的定义[J].刘安祥,汪传生译.橡胶技术与装备,1994,20(4):17-21.
[8]王明兰.一种新的橡胶炭黑分散性识别方法[J].控制理论与应用,2001,18(5):792-795.
[9]卢尚武,王晓辉.显微照相法测定炭黑分散度的研究[J].橡胶工业,1999,46(7):421-424.
[10]王明兰.炭黑在橡胶中分散性的模式识别(I)[J].华南师范大学学报(自然科学版),2000,18(3):56-61.
[11]王明兰.橡胶分散性的二维综合指标法[J].应用科学学报,2000,18(4):348-352.
[12]王明兰.胶料中炭黑分散性的Fisher判别法[J].橡胶工业,2000,47(9):551-554.
[13]王明兰.胶料中炭黑分散性的模糊判别法[J].橡胶工业,2001,48(5):302-305.
[14]王明兰.橡胶中炭黑分散度的自动判别[J].信息与控制,2002,31(1):59-61,67.