程安仁,林 浩,赵冬梅(北京首创轮胎有限责任公司,北京 100240)
提高胶料的抗撕裂性能和抗屈挠性能,降低轮胎胶料胶料生热,是提高轮胎高速性能、减少肩空和脱层的有效措施。本工作从提高胶料的抗撕裂性能和抗屈挠性能,降低肩胶生热的角度出发,探讨175GR白炭黑在载重轮胎胎肩胶中的应用。
1 实验
1.1 主要原材料
天然橡胶,SIR
20#,印度尼西亚产品;顺丁橡胶,BR9000,中国石化北京燕化石油股份有限公司产品;炭黑N326和炭黑N660,沙河市炭黑厂产品;白炭黑,牌号175GR,罗地亚白炭黑(青岛)有限公司产品;硅烷偶联剂Rsi-B,南京曙光化工总厂产品;其它原材料均为橡胶工业常用原材料。
1.2 配方
生胶(NR/BR) 100,氧化锌 8,硬脂酸 2,防老剂 2.5,硫化剂和促进剂 4,增塑剂 4,补强剂 变量(见表1),其它 1.15。
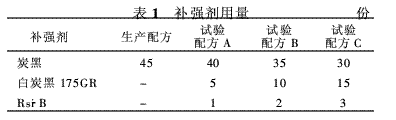
1.3 主要设备和仪器
1.57L密炼机,英国Banbury公司产品;Ф150 mm×320
mm开炼机,广东省湛江机械厂产品;F270型密炼机,英国Banbury公司产品;QLB-Q450型平板硫化机,湖州橡胶机械厂产品,MV2000型门尼粘度仪和MDR2000型硫化仪,美国孟山都公司产品;拉力机,XQ-250型,江苏省江都真武橡胶机械厂;压缩疲劳试验机,YS-25-Ⅱ型,上海化工机械四厂。
1.4 胶料混炼工艺
1·4·1 小配合试验
小配合试验胶料的一段混炼在1.57 L密炼机(转子转速115 r·min-1,压砣压力0.
35MPa)中进行混炼,加料顺序为:生胶→白炭黑、炭黑和小料→清扫→排胶(排胶温度145℃)。二段混炼在开炼机(速比为1:1·4)上,加料顺序为:一段混炼胶(停放16
h)→硫黄和促进剂→下片。
1·4·2 大配合试验
大配合试验胶料的混炼均在F270型密炼机内进行,工艺如下。
大配合试验胶料的母胶混炼在F270密炼机转子转速为40 r·min-1、压砣压力为0.6 MPa的条件下进行。
生产配方进行两段混炼,一段母胶的加料顺序为:生胶→炭黑和小料→软化剂→清扫→排胶,排胶温度160℃。
试验配方进行三段混炼,一段母胶的加料顺序为:生胶→白炭黑、部分炭黑和小料→软化剂→清扫→排胶,排胶温度150℃;二段母胶的加料顺序为:一段母胶→剩余炭黑→清扫→排胶,排胶温度153℃。
大配合胶料的终炼胶混炼均是在F270密炼机转子转速为20 r·min-1、压砣压力为0.6
MPa的条件下进行混炼,加料顺序为:母胶、小料→排胶,排胶温度105℃。
1.5 性能测试
门尼粘度按照ASTM D 1646-80方法进行测定;硫化特性按照ASTM D
2084-81方法进行测定;其它各项性能测试均按相应国家标准进行测定。
2 结果与讨论
2.1 理化分析
175GR白炭黑的理化分析结果见表2,可以看出,175GR白炭黑的理化性能达到指标要求。
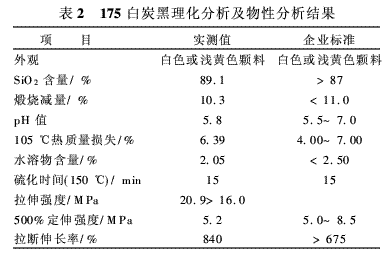
2.2 小配合试验
小配合试验结果见表3和表4。
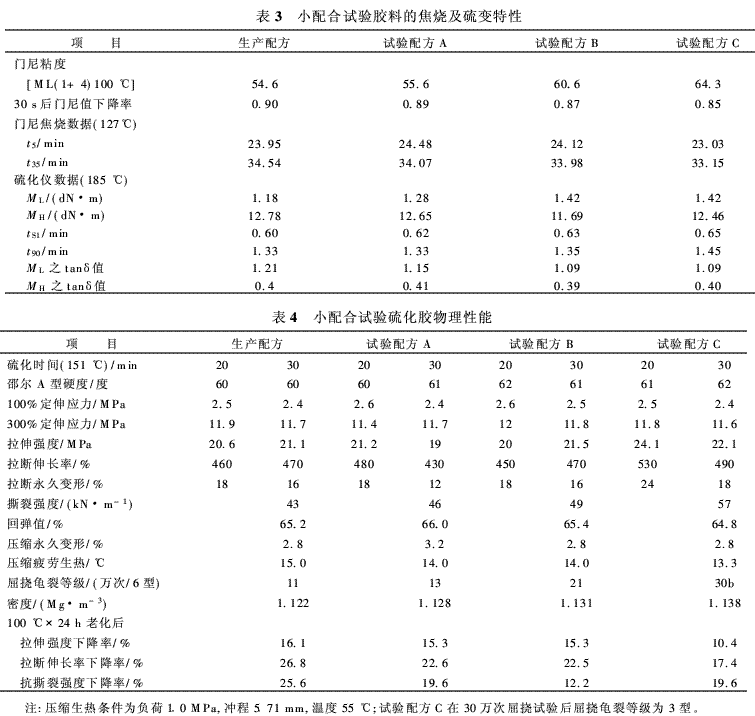
从表3可以看出,在相同的密炼工艺下,与生产配方胶料相比,试验配方胶料的门尼粘度较生产配方胶料大,而且随着白炭黑的用量增大而增大,在100℃下门尼结束后松弛30
s后的门尼粘度值下降率表明,白炭黑胶料的门尼粘度值下降率较生产配方胶料小,而且下降率随着白炭黑的用量增大而减小,表明加入白炭黑后胶料的流动性能变差,需要改善混炼工艺;在127℃下,试验配方胶料的门尼焦烧时间在白炭黑用量为5份时较生产配方略长,但随着白炭黑的用量延长,t5和t35有逐步缩短的趋势,这可能与Rsi-B用量增大有关;在185℃下,试验配方胶料焦烧时间tS1随白炭黑的用量增大逐步增大,正硫化时间t90也随白炭黑的用量增大逐步延长,而且均比生产配方胶料大,说明在此温度下,加入白炭黑硫化速度有变慢的趋势;从ML之tanδ值(表示未硫化胶在转矩达到最低时的tanδ值)来看,试验配方胶料均比生产配方胶料小,这表明试验配方胶料的混炼工艺性能较差,这与门尼松弛试验结果一致;从MH之tanδ值(表示硫化胶在转矩达到最高时的tanδ值)来看,试验配方胶料与生产配方胶料相当,这表明滚动阻力变化不大。
从表4可以看出,与生产配方胶料相比,试验配方胶料抗撕裂强度和抗屈挠性能明显提高,压缩疲劳温升有所降低,从老化后强度、拉断伸长率和抗撕裂强度的下降率来看,耐老化性能有所提高,其它性能基本相当。
从上述数据来看,加入175GR白炭黑后,除工艺性能和硫化速度需要进行调整外,其它性能都能达到或优于生产配方。
2.3 大配合试验
根据小配合试验结果,综合胶料的硫化性能和硫化机硫化测温数据,确定采用试验配方C进行大配合试验,同时对硫化体系稍加调整。为了改善试验配方C的工艺性能,我们将混炼工艺由普通胎肩胶的二段混炼改为三段混炼(见1.4节胶料混炼工艺)。大配合试验结果见表5和表6。
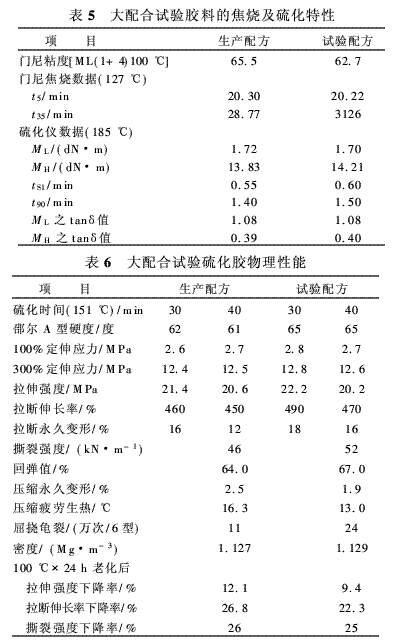
从表5可以看出,与生产配方胶料相比,试验配方胶料的门尼粘度略低,硫化速度稍慢,试验配方胶料的模量略大于生产配方胶料,焦烧时间和混炼工艺性能基本相同,滚动阻力也相当。
从表6可以看出,与生产配方硫化胶相比,试验配方硫化胶最显著的优点是:耐屈挠龟裂性能明显提高(涨幅118%),抗撕裂性能提高13%,回弹性能有所提高,压缩疲劳温升较低,压缩永久变形较小,硬度、定伸应力和拉断伸长率高于生产配方硫化胶,老化性能略好于生产配方硫化胶,其它性能基本相当。
另外,与生产配方胶料相比,试验配方胶料混炼时包辊性能良好,胶片表面平整、光亮,复合出型时粘合良好,挤出温度相当。
2.4 成品轮胎性能
结合公司试验安排,为了合理地利用资源,我们将试验胎肩胶和另一试验胎冠配方的胎冠胶同时进行成品试验并与生产配方成品进行对比,生产10·00-20
16PR试验轮胎6条,从中选取两条分别进行高速和耐久性能试验,试验结果见表7。
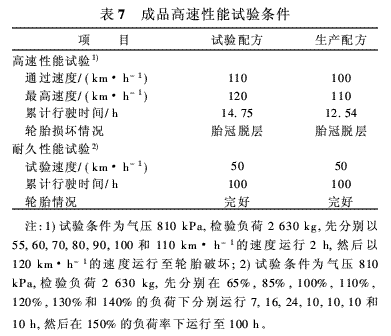
从表7可以看出,试验轮胎与正常轮胎相比试验轮胎的高速性能得到改善(提高一个速度级别),耐久性能相当。从损坏形式来看,两条轮胎均为脱空,而且均为胎冠胶与缓冲层脱空。就斜交轮胎而言,通过110
km·h-1检验,最高行驶速度达到120 km·h-1,已经算是斜交轮胎中的精品了。
2.5 效益分析
采用试验胎冠胶和试验胎肩胶配方生产的轮胎成本比采用生产配方生产的轮胎略有增长,如采用试验配方生产的每条10·00-20
16PR轮胎成本增长约3元。但试验配方胶料的工艺性能较好,轮胎高速性能显著提高,这对重视改进载重轮胎高速性能的今天具有重要的意义。
3 结论
采用175GR白炭黑与炭黑并用,可在降低载重轮胎胎冠胶生热的同时显著提高胎肩胶的耐屈挠龟裂性能和抗撕裂性能,回弹性能有所提高,硫化速度略有下降;随着胶料性能的改善,成品轮胎的高速性能也得到显著改善,提高了成品轮胎的性能价格比。
参考文献:略